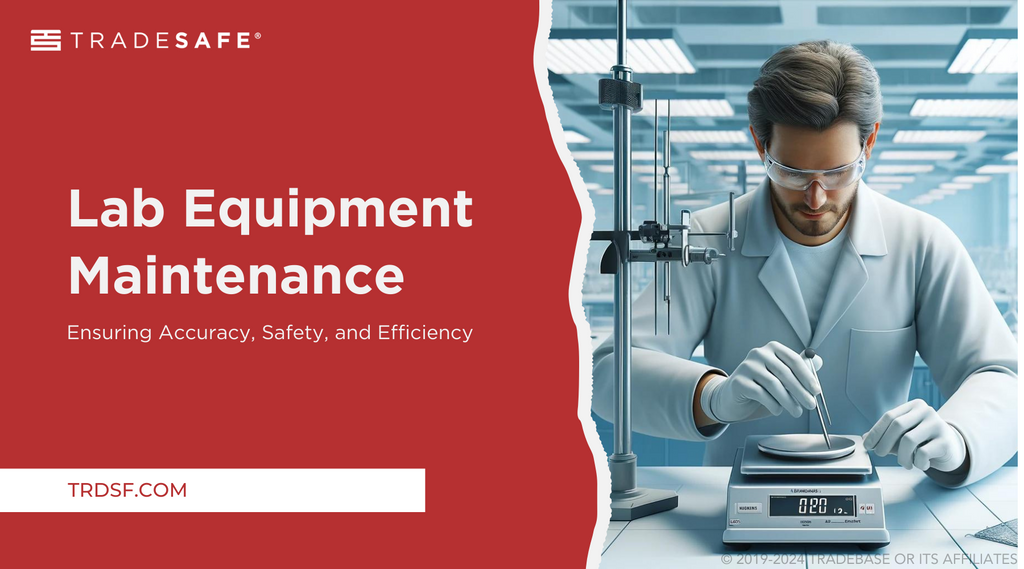
Laboratory equipment encompasses a wide range of tools and devices used by scientists and researchers to conduct experiments, collect data, and perform analyses across various scientific fields, including biology, chemistry, physics, and medicine. This lab equipment, from microscopes and centrifuges to spectrometers and pipettes, is fundamental for precise measurements, controlled experiments, and reliable results.
However, the smooth operation and reliability of this equipment hinge on a critical factor: proper laboratory equipment maintenance. Proper laboratory maintenance guarantees that equipment operates optimally, which leads to accurate results, prevents hazardous situations, reduces expensive repairs, and minimizes downtime, enhancing workflow efficiency.
Types of Laboratory Equipment Maintenance
Preventative Maintenance: Basic preventative maintenance involves scheduled inspections and routine tasks to prevent equipment failure before it occurs. This proactive approach includes cleaning, calibration, adjustments, and parts replacement according to the manufacturer’s guidelines.
Predictive Maintenance: Uses data and analytics to predict equipment failures before they happen. Techniques such as vibration analysis, thermal imaging, and fluid analysis help identify wear and tear, allowing for timely interventions. This method optimizes maintenance schedules based on actual equipment condition, rather than fixed intervals.
Corrective Maintenance: Occurs after equipment has already failed or shown signs of failing. It involves the repair or replacement of parts to restore the equipment to proper working order.
Condition-based Maintenance: Monitors the actual condition of equipment during its normal operation. By continuously checking operational parameters (like temperature and vibration), maintenance needs are addressed only when certain indicators show signs of deterioration.
Run-to-failure Maintenance: Equipment is deliberately used until it fails. While this might seem counterintuitive, it is practical for inexpensive or non-critical equipment where the cost of preventive maintenance would exceed the cost of replacing the entire unit.
Pillars of Effective Lab Equipment Maintenance
1. Preventive Maintenance
Preventative maintenance refers to a proactive strategy focused on regular inspection and maintenance of laboratory equipment to prevent future problems. This approach aims to keep equipment running efficiently and extend its operational lifespan. A preventive maintenance checklist is a comprehensive list of tasks and inspections designed to monitor, maintain, and ensure the proper operation of equipment before problems arise. This checklist serves as a structured guide for technicians to follow during routine maintenance visits, ensuring that no essential steps are missed. The checklist typically includes:
- Visual Inspections: Checking for any visible signs of wear, damage, or leaks.
- Cleaning: Ensuring that all parts of the equipment are clean and free from debris or contaminants that could affect functionality.
- Lubrication: Applying lubricants to moving parts to reduce friction and prevent wear.
- Adjustments: Making necessary adjustments to settings or alignments to ensure optimal performance.
- Part Replacements: Replacing worn or outdated parts that could potentially fail and cause equipment breakdowns.
- Safety Checks: Verifying that all safety features are functional.
- Calibration: Ensuring that instruments are producing accurate readings and outputs as expected.
- Testing: Running tests to verify that the lab equipment operates correctly.
2. Calibration
Calibration is the process of configuring an instrument to provide a result for a sample within an acceptable range. The accuracy of measurements and the quality of data generated by lab equipment hinge significantly on proper calibration. This ensures that the equipment performs correctly according to the established standards, which is critical for valid experimental results and compliance with scientific and regulatory guidelines.
Types of Calibration Procedures:
- Internal Calibration: This method involves using the equipment's built-in calibration functions to adjust its accuracy. Internal calibration is often convenient and quick, allowing for frequent checks without the need for external devices.
- External Calibration: This procedure uses certified reference materials and specialized external equipment to ensure the instrument's measurements are accurate. External calibration is typically performed by an accredited third party and is used when high levels of precision and compliance are required.
The frequency of calibration for lab equipment varies based on several factors, including the type of equipment, its usage rate, and specific regulatory requirements. Equipment that is highly sensitive or used frequently generally requires more regular calibration to ensure accuracy and reliability. Regulatory standards also dictate calibration intervals, particularly in fields where precise measurements are critical for quality control and safety.
3. Documentation
Record keeping of all maintenance activities is essential for effective laboratory management. Documentation ensures that every Interventions and adjustments made to laboratory equipment are tracked, providing a clear history that can be crucial for troubleshooting, compliance audits, and planning future maintenance. Detailed record keeping also supports warranty claims and helps maintain the validity of experimental results by demonstrating laboratory staff maintain equipment properly.
Elements of a comprehensive equipment maintenance log:
- Equipment Details: Includes the model, serial number, and manufacturer of each piece of equipment. This information is crucial for tracking and managing inventory as well as for referencing specific lab equipment in maintenance schedules and manuals.
- Specific Maintenance Tasks Performed: Records should specify whether the maintenance involved cleaning, calibration, repairs, or other tasks. Detailing the nature of the maintenance helps in understanding the lab equipment’s maintenance history and planning future interventions.
- Date and Time of Each Maintenance Activity: Logging the exact date and time of maintenance activities helps in tracking the frequency of maintenance and is essential for adhering to scheduled maintenance intervals.
- Technician Responsible for Performing the Maintenance: Identifying who performed the maintenance ensures accountability and allows for follow-ups if there are questions or issues related to the work done.
- Any Observations or Issues Noted During Maintenance: Recording any irregularities or problems observed during maintenance activities can be critical for the early detection of potential issues and can guide future maintenance decisions.
4. Safety Considerations
Prioritizing safety during all laboratory maintenance procedures is crucial to prevent accidents and ensure the well-being of the personnel. Laboratory environments contain various hazards, and maintenance activities can expose technicians to increased risks if not managed correctly.
Potential hazards associated with specific equipment types:
- Electrical Hazards: Lab equipment like autoclaves, centrifuges, and heating devices can pose electrical risks, especially if maintenance involves interacting with electrical components.
- Radiation Exposure: Devices such as X-ray machines and certain types of spectrometers emit radiation, which requires strict safety protocols during both use and maintenance.
- Chemical Spills: Handling and maintaining equipment like chromatography and chemical reactors can lead to exposure to hazardous chemicals, necessitating careful handling procedures, such as a Chemical Hygiene Plan (CHP).
Importance of proper training and Personal Protective Equipment (PPE):
- Training: Every lab technician must receive thorough training on the specific safety protocols related to the equipment they maintain. This training should cover the correct procedures for safely performing maintenance tasks, including how to handle emergencies.
- Personal Protective Equipment: Using the appropriate PPE, such as gloves, goggles, lab coats, and sometimes respirators, is essential. PPE provides a physical barrier against chemical, biological, mechanical, or radiological threats that might arise during lab maintenance tasks.
General Tips for Laboratory Equipment Care
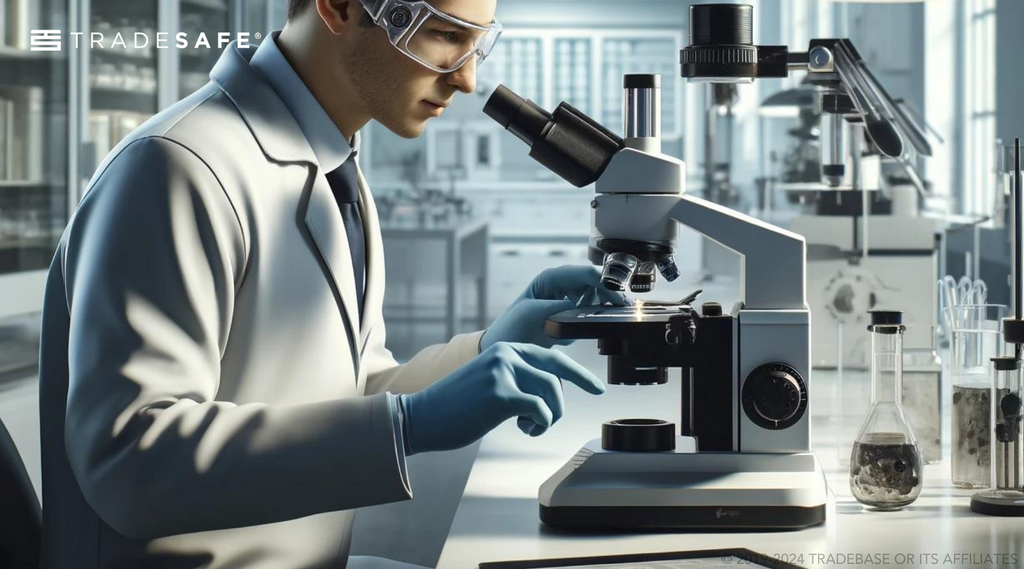
Proper daily care and handling of lab equipment are crucial to maintaining its functionality and extending its lifespan. Below are some practical tips for general care:
- Regularly clean all equipment to prevent the buildup of dust, chemicals, and biological materials. Use appropriate cleaning solutions recommended for each type of equipment, and ensure that sensitive components are handled with care to avoid damage.
- Store all equipment in appropriate conditions. For example, sensitive instruments should be kept in dry, dust-free environments to prevent corrosion or other damage. Ensure that all items are properly covered or placed in cabinets when not in use.
- Implement and enforce strict lab safety protocols when handling laboratory equipment and hazardous materials. This includes using appropriate PPE and adhering to safety guidelines for chemical handling.
- Do not overload equipment such as centrifuges or heating elements beyond their recommended capacity. Overloading can lead to malfunctions, reduced efficiency, and potential safety hazards.
- Always handle equipment with care to avoid dropping or jarring instruments that are sensitive to shock or vibration. This is particularly important for precision instruments like balances and microscopes.
- Adhere to the manufacturer's instructions for use, maintenance, and storage. These guidelines are designed to optimize the performance and safety of the equipment.
- Periodically inspect equipment for any signs of wear, malfunction, or damage. Early detection of problems can prevent more serious issues and costly repairs.
- Encourage personnel to promptly report any signs of equipment malfunction or unusual behavior. This not only helps in timely maintenance but also prevents potential accidents and ensures the reliability of experimental results.
Maintenance Requirements of Common Laboratory Equipment
Here’s what you need to know about the maintenance of some commonly used laboratory instruments:
- Microscopes: Regular cleaning of the microscope lenses is critical to prevent blurry images, which can lead to inaccurate measurements. Use lens tissue or a proper optical cleaner to gently remove dust or oil residues without scratching the lenses.
- Centrifuges: Always ensure that centrifuge tubes are balanced across from one another to prevent damage to the machine and ensure accurate separation of samples. Imbalances can cause vibrations, noise, and potentially harm the centrifuge motor or rotor.
- Balances: Regularly calibrate equipment like analytical balances to ensure precise weighing results. Calibration should be performed according to the manufacturer’s guidelines, typically after relocation, environmental changes, or on a scheduled basis.
- Pipettes: Regular maintenance and calibration are crucial for pipettes to deliver volumes accurately. This is especially important for experiments requiring precise measurements of liquids. Consider professional servicing annually or biannually, and practice daily checks for accuracy.
- Safety Lab Equipment: Maintenance of safety laboratory equipment, such as eyewash and shower stations and fume hoods, is critical not only for the functionality of the equipment but also for the safety of lab personnel. Maintenance of eyewash stations includes regular testing to ensure proper function, cleaning to prevent microbial contamination, and checking that the water flow is adequate and accessible. Fume hoods require frequent checks to ensure that airflow and filters are functioning correctly to protect users from inhaling hazardous chemicals.
FAQs on Laboratory Equipment Maintenance
Why is preventive maintenance so important in the laboratory?
Preventive maintenance is crucial in laboratories to ensure that all equipment operates efficiently and accurately, which is important for achieving reliable results in scientific research. This proactive approach helps avoid unexpected equipment failures that can disrupt experiments, lead to data loss, or cause safety hazards, ultimately saving time and reducing costs.
Why is it important to maintain logs on lab and safety equipment?
Maintaining an equipment maintenance log on lab and safety equipment is important for several reasons: it ensures compliance with regulatory standards, helps in tracking the performance and maintenance history of the equipment, facilitates troubleshooting and repairs, and supports quality assurance and audit processes. A detailed equipment maintenance log also provides invaluable data for making informed decisions about equipment upgrades or replacements.
What are the challenges in food lab equipment maintenance?
Maintaining lab equipment in the food industry poses unique challenges due to the stringent cleanliness and sterilization standards required to prevent contamination. Equipment used in food labs often requires frequent and meticulous cleaning, and there's a need for precise calibration to ensure accurate measurements of nutritional content and contaminants. Compliance with food safety regulations also demands rigorous documentation and regular audits.
What is laboratory management and maintenance?
Laboratory equipment management and maintenance refer to the processes and practices involved in organizing and controlling laboratory resources and operations to ensure efficient, safe, and effective functioning. This includes equipment procurement, maintenance scheduling, safety training, compliance with standards, and the management of human resources and finances.
How do you schedule equipment maintenance?
Scheduling equipment maintenance involves creating a systematic plan based on the manufacturer’s recommendations, the equipment’s usage patterns, and any regulatory requirements. Most laboratories use maintenance management software to automate reminders and track maintenance activities. Regular reviews of an equipment maintenance log help adjust the schedule based on actual needs and performance, ensuring that all equipment remains in optimal condition.