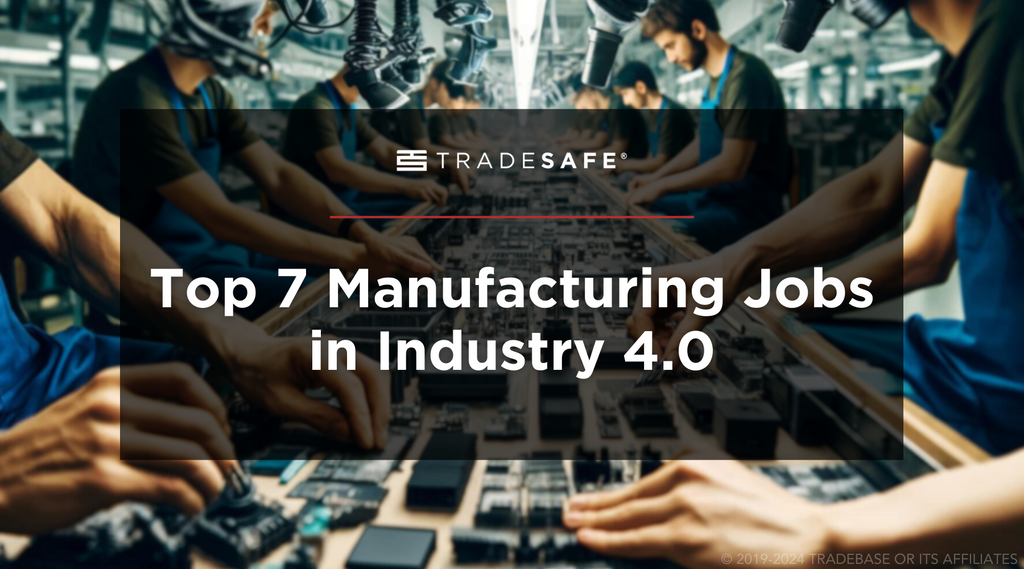
The rise of automation in manufacturing is an undeniable force in the fourth industrial revolution. Robots with increasing proficiency, coupled with intelligent systems powered by artificial intelligence (AI) and the Internet of Things (IoT), are transforming production lines. While concerns about manufacturing automation jobs displacement are valid, this shift also presents exciting opportunities. Understanding this changing landscape is crucial for both businesses and workers.
This article delves into the top 7 manufacturing jobs in Industry 4.0, a world where automation and human ingenuity co-exist.
The Impact of Automation on Manufacturing Jobs
Job Displacement
Automation in manufacturing is reshaping the landscape of the workforce. According to the World Economic Forum's Future of Jobs Report, by 2025, automation is projected to displace about 85 million jobs globally. These are typically roles that involve repetitive tasks, such as those found on assembly lines or in basic machine operations, which can be more efficiently carried out by machines or robots.
Job Creation
While the figure for job displacement may seem daunting, it's not all grim news. The same report from the World Economic Forum suggests that automation is also set to create approximately 97 million new roles by 2025. These new jobs will likely arise in areas like robot maintenance, data analysis, and the development of automation technologies, which require more complex, technical skills than the jobs they replace.
The Skills Gap
The transformation driven by automation not only creates new jobs but also demands new skills. As the industry grows and an older generation of workers (the baby boomers) retires, a significant skills gap is emerging. This presents a dual challenge for the manufacturing industry: recruiting employees who can handle new technologies and retaining them as the workplace and its demands continue to evolve.
Reskilling and Upskilling the Manufacturing Workforce
As the manufacturing automation landscape evolves, the need for reskilling and upskilling the workforce becomes increasingly vital. This shift is not just about keeping jobs but enhancing them. Equipping workers with new skills ensures they can adapt to new roles that automation may create, securing their positions and enabling them to contribute more effectively to a technologically advanced environment.
There are several types of training programs and initiatives that can help bridge the skills gap in advanced manufacturing:
- On-the-Job Training: Many companies implement on-the-job training programs to teach workers how to operate new machinery or use new software. This hands-on approach is beneficial for practical learning and immediate application.
- Partnerships with Educational Institutions: Some manufacturing companies partner with local colleges and technical schools to design courses that fit the specific needs of the industry. These partnerships can offer certifications or even degree programs in fields like robotics, data analytics, and computer-aided design.
- Online Courses and Workshops: With the rise of digital education platforms, many workers turn to online courses that offer flexible learning schedules. These can range from specific skills, like programming languages, to broader courses on engineering principles or automation technology.
- Apprenticeship Programs: Combining instruction with on-the-job training, apprenticeship programs are a comprehensive approach to teaching the skills that workers need today and in the future. These programs often lead to full-time positions within the company.
While technical skills are important, the significance of human skills like critical thinking, problem-solving, and adaptability should not be overlooked. These skills enable workers to handle complex situations that machines cannot, especially when dealing with unexpected issues or when innovation is required.
7 High Demand Careers in Smart Manufacturing
The shift in Industry 4.0 not only revolutionizes production processes but also dramatically alters the job landscape, creating demand for new skill sets. Here, we explore some key careers that are becoming essential in this new era of smart manufacturing:
Data Scientists
Role and Importance: In a smart manufacturing setting, data scientists analyze vast amounts of data generated from manufacturing processes to identify patterns, predict outcomes, and improve efficiencies. Their work supports decision-making and strategic planning, helping companies stay competitive in a rapidly evolving industry.
Skills Required: Data scientists need a strong foundation in statistics and machine learning. Proficiency in programming languages such as Python or R is crucial. They also need to have an understanding of data management tools and experience in visualizing and interpreting complex data sets.
IoT Engineers
Role and Importance: Internet of Things (IoT) engineers are critical in connecting various devices and machines in an advanced manufacturing environment. By designing and implementing IoT solutions, they enable real-time data collection and communication between equipment, which enhances automation and machine monitoring capabilities.
Skills Required: IoT engineers must be knowledgeable in network security, systems engineering, and data analysis. They also need a solid background in electronics and software development, as well as an understanding of cloud platforms that support IoT architecture.
Smart Factory Managers
Role and Importance: Smart factory managers oversee operations of advanced technologies like robotics, IoT, and artificial intelligence in manufacturing. They ensure that all parts of the production process are harmonized and optimized. Their leadership directly influences productivity, efficiency, and innovation.
Skills Required: This role requires a blend of technical and managerial skills. A deep understanding of smart technologies, along with skills in project management, operations management, and strategic planning, are necessary. Effective communication and leadership abilities are also vital.
Robotics Engineers and Technicians
Role and Importance: Robotics engineers and technicians design, build, and maintain the robots used in manufacturing automation processes. Their expertise supports the deployment of robots that can perform tasks with precision and efficiency, often in environments that are hazardous for human workers.
Skills Required: Knowledge of mechanical and electrical engineering is essential, along with programming skills for robot control systems. Experience with CAD software for designing robotic systems and an understanding of the latest advancements in robotics are also important. Another significant aspect of their role now includes working with collaborative robots in manufacturing. These cobots are designed to work alongside human workers, often in shared spaces, without the need for safety cages.
Smart Safety Supervisors
Role and Importance: As advanced manufacturing environments become more complex with the integration of various technologies, the role of smart safety supervisors becomes more critical. They ensure that all smart technologies are implemented and operated in a way that upholds safety standards, protecting both human workers and machinery.
Skills Required: Knowledge of safety regulations specific to the manufacturing process and an understanding of automated systems are crucial. Skills in risk assessment, emergency response planning, and the ability to train others on safety protocols are also important.
Smart QA Managers
Role and Importance: Quality assurance in manufacturing automation is evolving with technology. Smart QA managers use data analytics and automated systems to enhance product quality checks. They are responsible for setting quality standards and ensuring that products meet these criteria consistently.
Skills Required: Attention to detail and a strong understanding of manufacturing processes are essential. Proficiency in using advanced QA technologies and data analysis tools to monitor quality in real-time is also crucial.
Cybersecurity Professionals
Role and Importance: As manufacturing facilities become more interconnected, they also become more vulnerable to cyber threats. Cybersecurity professionals protect sensitive data and ensure that networked systems are secure against attacks, which is crucial for maintaining operational integrity and safeguarding proprietary information.
Skills Required: A robust understanding of information security, network protocols, and encryption. Skills in threat assessment, incident response, and security audits are critical. Awareness of the latest cybersecurity trends and threats is also essential.
What is the Next Big Thing in Manufacturing Automation?
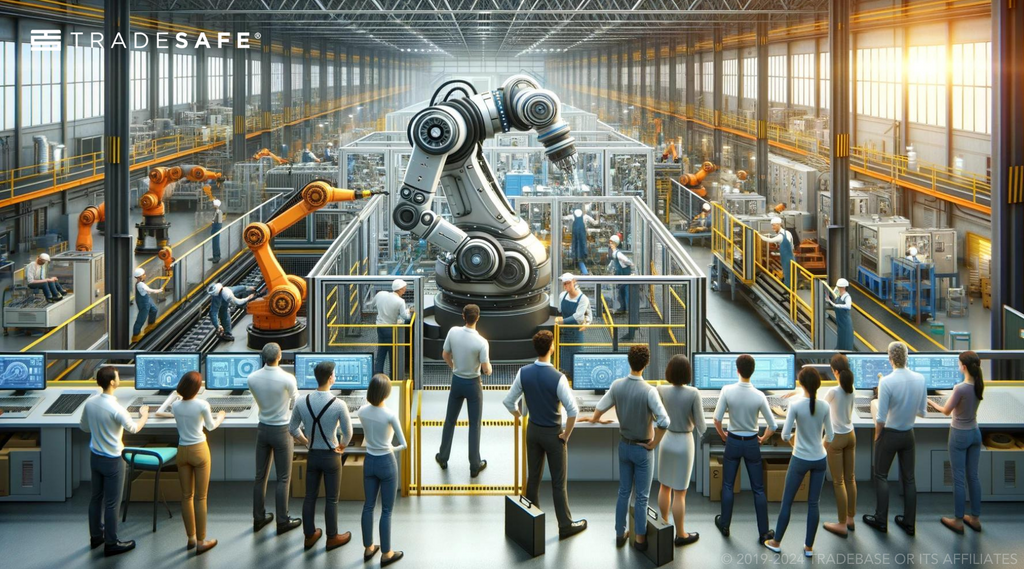
Cloud-native platforms represent a significant shift in how manufacturing operations are managed and scaled. Unlike traditional IT infrastructure, cloud-native applications are designed to exist and operate in the cloud, offering flexibility, scalability, and resilience. They allow manufacturing operations to be more agile, with easier integration of new technologies such as AI and IoT.
These platforms can dynamically adjust to demand, improve disaster recovery, and enhance collaboration across global teams. They also reduce the overhead and limitations associated with maintaining physical IT infrastructure, enabling manufacturers to focus more on core business operations and innovation.
Other Industrial Manufacturing Trends
Technology Investment
According to Deloitte’s 2023 outlook survey, leading manufacturers are focusing their investments in three main areas: robotics and automation (62%), data analytics (60%), and the Internet of Things (39%). Notably, technologies like blockchain and quantum technology are currently viewed as lower priorities, receiving minimal focus from the industry.
The integration of the Industrial Internet of Things (IIoT) is particularly noteworthy, with about 10% of manufacturers having adopted this technology by 2020. Predictions by Grand View Research suggest this figure will rise to around 50% by 2025, indicating a significant shift towards interconnected manufacturing environments.
Talent Acquisition and Retention
A survey of U.S.-based manufacturing leaders highlighted that 83% consider attracting and retaining workers a top priority. As per McKinsey, the demand for traditional physical labor skills in manufacturing is expected to decrease by 30% over the next decade, while the need for technical skills is projected to increase by 50%. This shift underscores the importance of redefining talent management strategies to focus on upskilling employees in digital and technical competencies.
Sustainability Investment
A 2022 study by Climate Impact Partners reveals that 42% of Fortune Global 500 companies have achieved significant climate milestones or have committed to doing so by 2030. In the manufacturing sector, investments are being channeled into smart building technologies that employ sensors to control heating, cooling, and lighting systems more efficiently.
Additionally, manufacturers are increasingly turning to renewable energy sources for their operations and are incorporating electric vehicles for the transportation of raw materials and finished products, motivated in part by clean vehicle tax credits.
Reassessing the Supply Chain
The global disruptions experienced in recent years, such as the COVID-19 pandemic, have prompted manufacturers to critically reassess their supply chain models. Companies are looking to enhance supply chain resilience by diversifying suppliers, increasing inventory buffers, and implementing more comprehensive risk management strategies. These changes are designed to make supply chains more agile and less susceptible to disruptions, ensuring a steady flow of materials and products.
Developing the Factory of the Future
The "factory of the future" concept is shaping up to be a cornerstone of modern manufacturing, characterized by high levels of digitization and interconnectivity. These factories leverage advanced technologies such as AI, machine learning, and digital twins to optimize operations. The goal is to create highly flexible and efficient manufacturing environments that can swiftly adapt to market changes and consumer demands, thus driving greater productivity and innovation.
Smart Manufacturing Jobs FAQs
Is Industry 4.0 good or bad?
Industry 4.0 is largely positive, enhancing efficiency and competitiveness in manufacturing. It does, however, require significant investments and raises concerns about potential job losses due to automation.
What big difference will the concept of Industry 4.0 make?
Industry 4.0 introduces digital integration into manufacturing, leading to smarter production, better supply chain management, and increased responsiveness to customer needs, fundamentally changing factory operations.
What is the manufacturing industry outlook for 2024?
The outlook for 2024 is cautiously optimistic. Despite ongoing challenges like supply disruptions and labor shortages, advancements and increasing adoption of Industry 4.0 are expected to drive growth.
What industry is most affected by automation?
The automotive industry is heavily affected by automation, with robotics and automated processes significantly enhancing the efficiency and reducing costs in vehicle manufacturing.
Which industry cannot be automated?
Industries that require complex human interactions and emotional intelligence, such as advanced healthcare, social work, and certain aspects of education, are less prone to full automation. These fields depend on empathy and interpersonal skills, which current technology cannot fully replicate.
TRADESAFE is a leader in providing premium industrial safety solutions, including Lockout Tagout Devices, Workplace Signs, and more; all precision-engineered to meet and exceed rigorous safety standards.