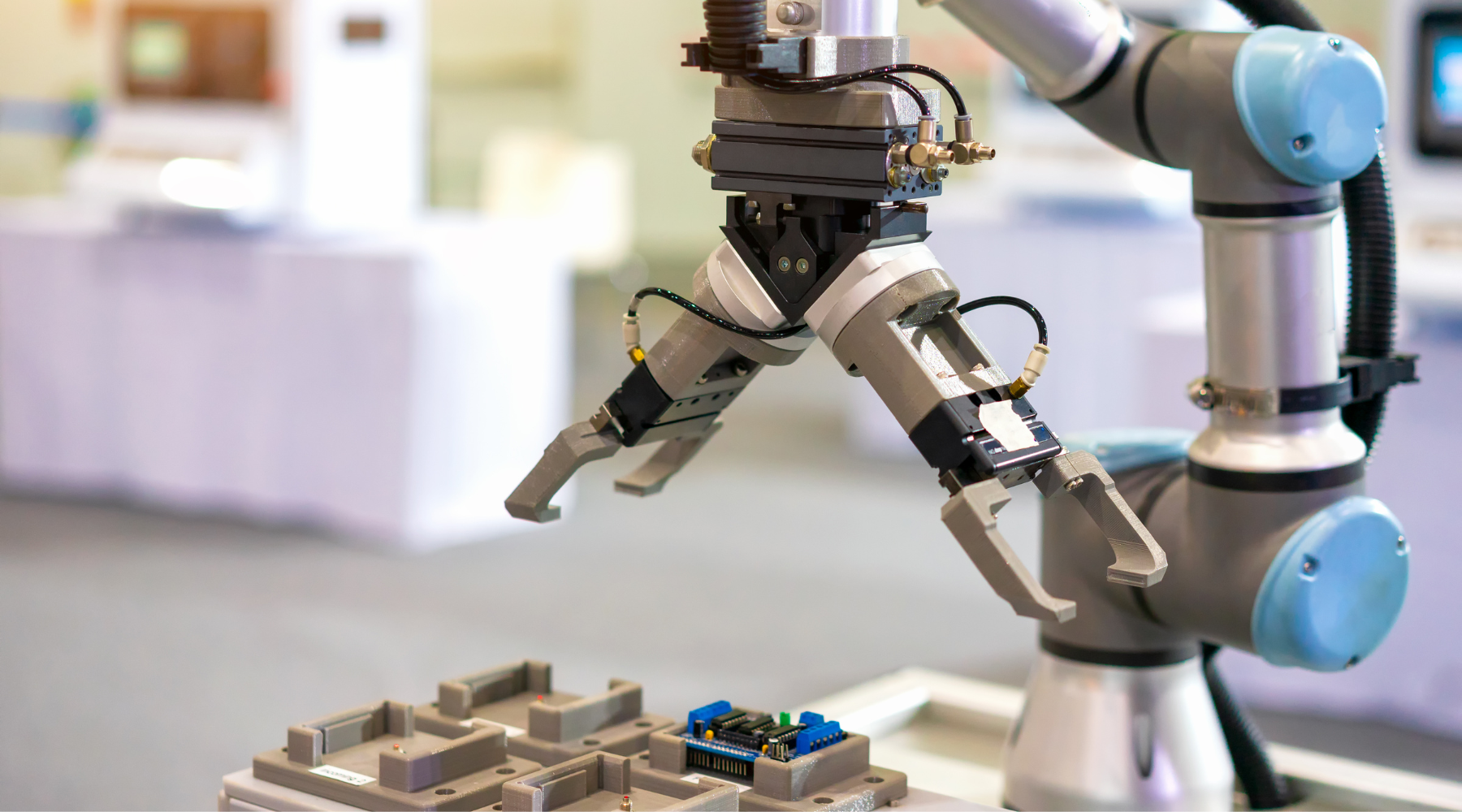
What Are Grippers?
Grippers play a crucial role in various industrial automation processes, enabling robots to handle objects with precision and efficiency. In this comprehensive guide, we will delve into the world of grippers, exploring their definition, purpose, and the significance they hold in industrial automation.
Grippers are mechanical devices designed to hold, grasp, and manipulate objects. They are commonly used in robotic systems to facilitate tasks such as picking up, placing, and moving objects with precision. Grippers provide the necessary interface between the robot and the object it interacts with, allowing for effective manipulation in manufacturing, assembly, and other industrial processes.
How Do Grippers Work?
Grippers utilize various mechanisms and actuation systems to perform their tasks. Mechanical grippers, which are commonly used, feature jaws that can open and close to grip objects. Pneumatic, hydraulic, and electric grippers employ different types of actuators to achieve the gripping action. By applying force and controlled movements, grippers securely hold objects, ensuring stability and control during robotic operations.
Importance of Grippers in Industrial Automation
Grippers are integral components of industrial automation, revolutionizing manufacturing processes across multiple industries. Their ability to handle objects efficiently, adapt to various shapes and sizes, and operate in diverse environments makes them indispensable in the following ways:
Increased Efficiency: Grippers enable robots to perform tasks with speed and precision, enhancing production throughput and reducing cycle times. They allow for the automation of repetitive and labor-intensive processes, minimizing human error and increasing overall efficiency.
Flexibility and Adaptability: Grippers are designed to accommodate a wide range of object sizes, shapes, and materials. This versatility allows for the handling of diverse products, enabling robots to adapt to different production requirements and improve production line flexibility.
Improved Safety: By taking over repetitive and physically demanding tasks, grippers help ensure the safety of human workers. They minimize the risk of injuries associated with manual handling, particularly in hazardous environments such as heavy machinery or toxic substances.
Types of Grippers
Grippers come in various types, each designed for specific applications and requirements. Understanding these types will provide insights into the diverse capabilities and functionalities of grippers.
Mechanical Grippers
Mechanical grippers are widely used due to their simplicity, reliability, and cost-effectiveness. They employ mechanical linkages to open and close their jaws, securely gripping objects. The following subtypes of mechanical grippers exist:
- Two-Jaw Mechanical Grippers: These grippers feature two opposing jaws that close symmetrically to grip objects.
- Three-Jaw Mechanical Grippers: Grippers with three jaws offer improved gripping stability by evenly distributing the gripping force.
- Angular Grippers: Angular grippers employ a pivoting mechanism to grip objects at different angles, offering versatility in manipulation.
- Parallel Grippers: Parallel grippers consist of two parallel jaws that move together to grip objects, providing a firm and consistent hold.
Pneumatic Grippers
Pneumatic grippers operate using compressed air to generate the gripping force. They are known for their fast response times and high gripping forces, making them suitable for applications requiring quick and powerful gripping actions.
Hydraulic Grippers
Hydraulic grippers utilize hydraulic fluids to generate the gripping force. They offer high gripping forces and are commonly used in heavy-duty applications where substantial force is required.
Electric Grippers
Electric grippers employ electric motors or solenoids to achieve the gripping action. They provide precise control over gripping force, speed, and position, making them suitable for applications that require delicate handling or where force feedback is crucial.
Internal Vs External Gripping
In addition to the various types of grippers, another important aspect to consider is the distinction between internal and external gripping. Internal gripping involves the gripper enclosing the object entirely, securely holding it within the gripper's jaws or fingers. This type of gripping is suitable for objects with a defined shape or those that can be fully contained within the gripper.
On the other hand, external gripping refers to the gripper gripping the object from the outside, typically by clamping onto its edges or surface. This method is applicable when the object's shape or fragility makes it impractical or impossible to be fully enclosed.
What is a Rotary Actuator?
A rotary actuator is a crucial component often integrated with grippers to provide additional functionality. It enables grippers to rotate or swivel, allowing for better orientation and positioning of objects during handling. Rotary actuators can be pneumatic, hydraulic, or electric, depending on the specific application requirements.
Tooling/Finger Design Considerations
The design of gripper tooling or fingers plays a vital role in the successful handling of objects. Factors such as object shape, weight, and surface characteristics must be taken into account to ensure a secure grip without causing damage.
Considerations for gripper tooling/finger design include selecting appropriate materials, incorporating features like sensors for object detection and force feedback, and optimizing the shape and size of the fingers to match the object's contours.
FAQs
1. What is the typical lifespan of a gripper?
The lifespan of a gripper depends on various factors, including its quality, usage frequency, and the operating environment. High-quality grippers with regular maintenance can last for several years, while others may require replacement or repairs more frequently.
2. Can grippers be customized for specific applications?
Yes, grippers can be customized to meet specific application requirements. Manufacturers often provide options for different finger styles, sizes, and materials to suit diverse objects and operational needs.
3. How do grippers contribute to productivity improvement?
Grippers enhance productivity by automating repetitive tasks, reducing human intervention, and enabling faster and more precise object handling. They help streamline production processes, increase throughput, and minimize errors, ultimately improving overall productivity.
4. Are grippers safe to use in collaborative robot setups?
Yes, grippers designed for collaborative robots prioritize safety. They incorporate features like force and torque sensors, collision detection, and compliance mechanisms to ensure safe interaction between robots and humans.
5. What are the cost considerations for gripper procurement?
The cost of grippers varies depending on their type, capabilities, and quality. Pneumatic grippers tend to be more affordable, while electric grippers and specialized grippers may have higher costs. It is essential to consider the specific requirements of the application and balance them with budget constraints when selecting a gripper.