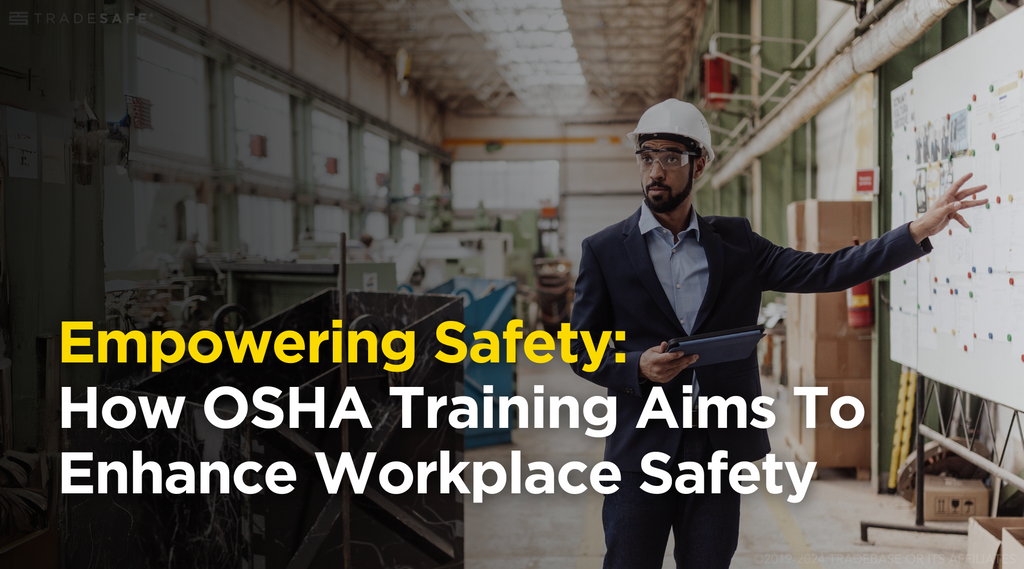
In an effort to ensure and enhance employee workplace safety, the Occupational Safety and Health Administration (OSHA) is holding a three-day training program for federal agencies to educate personnel on key health and safety topics, this coming August 6 to 8, 2024 in Arlington Heights, Illinois. The training event is done in partnership with the agency’s Office of Federal Agency Programs and is available free of charge to federal agency personnel and employees.
What is OSHA Training?
OSHA training offers critical education on how to recognize, reduce, and eliminate workplace hazards. It includes a range of topics from how to use personal protective equipment to strategies for minimizing exposure to hazardous substances. This free OSHA training course is not just about following regulations; it's about building a culture of safety and awareness among workers and employers alike.
Key Safety and Health Topics in OSHA Employee Workplace Safety Training
OSHA’s workplace safety training covers a wide array of safety and health topics that are crucial for maintaining a safe work environment. The goal of free OSHA training programs is to educate employees with vital knowledge and know-how that will help ensure their safety on various occasions and events. Here’s a closer look at some of the essential areas of federal employee workplace safety:
Verbal De-escalation Techniques
Conflict can arise in any workplace setting. Verbal de-escalation techniques are crucial for managing and resolving conflicts peacefully. In federal work, conflict resolution through de-escalation strategies is critical. This OSHA training teaches employees how to effectively communicate and defuse potentially dangerous situations before they escalate, focusing on maintaining calm, using non-confrontational body language, and actively listening to the concerns of others.
Control of Hazardous Energy (Lockout/Tagout)
The control of hazardous energy, commonly known as lockout/tagout procedures, is vital for preventing accidents and injuries. This training focuses on specific practices and procedures to safely shut down and lock out machinery during maintenance and servicing. It ensures that machines are properly shut off and cannot be started up again until the completion of maintenance or repair work, thereby protecting workers from the release of hazardous energy.
Forklift Operation and Material Handling
Forklifts and other material-handling equipment are common in many industries but can be extremely dangerous if not operated correctly. OSHA training covers the safe operation of forklifts, emphasizing proper driving techniques, load handling, vehicle maintenance, and understanding the limitations of the equipment.
Electrical Safety
Electrical hazards are one of the leading causes of workplace injuries and fatalities. Electrical safety training includes identifying potential risks, proper procedures for working with or near electrical components, and the use of protective equipment. It also teaches workers how to respond in the event of an electrical emergency.
Fire Protection
Fire protection training is essential in preventing fire emergencies and ensuring the safety of all personnel. It includes proper use of fire extinguishers, understanding the different types of fires, evacuation procedures, and the maintenance of fire-safe environments within the workplace.
Emergency Preparedness in the Federal Workplace
Specifically tailored for employees in federal workplaces, this training covers unique protocols for handling emergencies, including natural disasters, security threats, and other unexpected incidents. It emphasizes the importance of having a clear plan and role assignments to ensure safety and minimal disruption during emergencies.
Scaffolding in Construction Overview
Scaffolding safety is crucial, particularly in construction environments. This training addresses the setup, use, and disassembly of scaffolding, highlighting the importance of regular inspections to prevent falls and other injuries associated with scaffold use.
Bloodborne Pathogens
his workplace safety training course is particularly designed for workers who could be exposed to blood or other infectious materials. It covers the proper handling of these materials, precautions to prevent virus exposure, and procedures for what to do if exposure occurs, including the importance of vaccination and post-exposure protocols.
Effective Respiratory Protection Programs
Respiratory protection is necessary for workers exposed to harmful dusts, fogs, smoke, mists, gases, vapors, and sprays. Respirator training covers the selection, use, care, and maintenance of respirators, ensuring that workers are not exposed to potentially life-threatening conditions.
Exposure to Silica Dust or Quartz Dust
Exposure to silica dust can lead to serious respiratory diseases. Training focuses on identifying silica hazards, understanding the health risks, and learning proper job practices to reduce exposure, such as using engineering controls, following proper work practices, and wearing appropriate personal protective equipment.
Developing a Safety Program in the Workplace
Developing an effective safety program in the workplace is crucial for ensuring employee well-being and productivity. It starts with a strong commitment from leadership, who must prioritize safety, allocate resources, and involve employees in shaping safety policies. Regular hazard identification and risk assessment, along with continuous workplace safety training and education, form the backbone of the program, ensuring all employees are equipped to handle potential dangers. Implementing appropriate workplace controls and having a clear emergency response plan further mitigate risks and prepare employees for potential crises.
Clear, written health and safety program and policies that outline the responsibilities of everyone within the organization are essential. These policies should be accessible and regularly updated. Regular communication through various channels like newsletters and meetings helps keep safety a priority, and a system for regular program evaluation and improvement ensures that safety measures remain effective and relevant. Recognizing and rewarding employees for safe practices can also reinforce the importance of adherence to safety protocols, promoting a culture of safety that pervades every level of the organization.
Implementing comprehensive health training and specialized training programs is essential for controlling hazards in the workplace and fostering a proactive approach to safety. These programs not only protect employees by providing the knowledge and tools needed to avoid creating hazards but also contribute to the overall effectiveness of workplace health programs. By prioritizing safety through such educational efforts, organizations can ensure a safer, healthier environment where employees feel valued and protected
FAQs
How does a well-implemented safety and health program affect employee retention?
A well-implemented safety and health program can significantly improve employee retention by creating a safer and more secure workplace. Employees are more likely to stay with a company that demonstrates a commitment to their well-being and safety. A well-implemented safety and health program can significantly improve employee retention by creating a safer and more secure workplace. Employees are more likely to stay with a company that demonstrates a commitment to their well-being and safety.
Is OSHA training worth it?
Yes, OSHA training is worth it. It not only helps prevent workplace injuries and fatalities by educating employees on safety practices and standards but also enhances overall workplace efficiency and compliance with legal requirements.
Does OSHA require employees to be trained?
Yes, OSHA requires employees to be trained on specific safety and health standards that apply to their job functions. The extent and type of training depend on the particular risks associated with their roles.
What is the federal law for workplace safety?
The federal law for workplace safety is outlined in the Occupational Safety and Health Act of 1970. It requires employers to provide a safe and healthful workplace free from recognized hazards and to comply with OSHA standards and regulations.