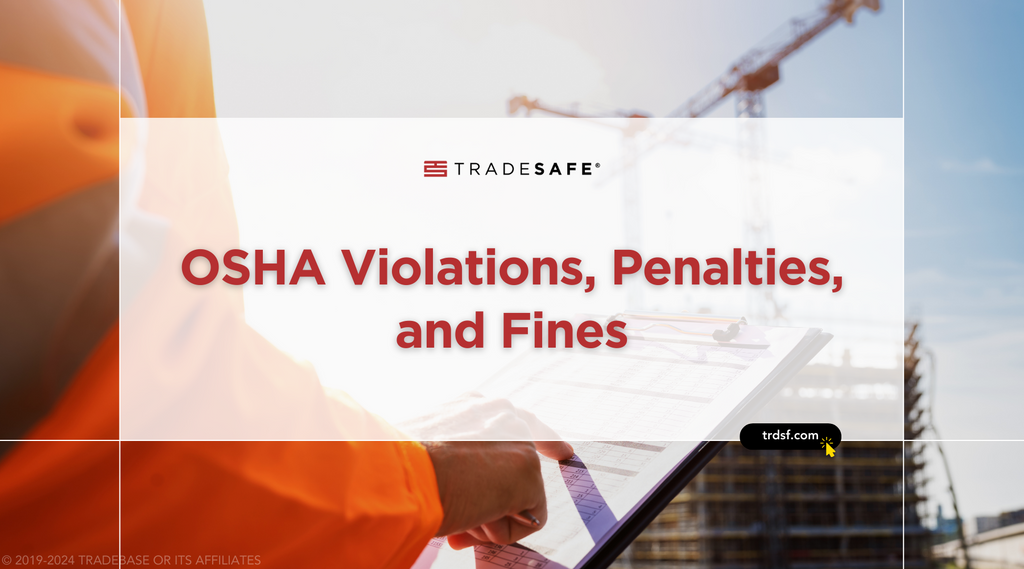
The Occupational Safety and Health Administration, commonly referred to as OSHA, is a federal agency that levies fines for businesses violating standard employee safety protocols. These fines are exacted to make employers strengthen their mission of ensuring safe and healthy working conditions for employees.
This article covers all 6 types of violations and their corresponding monetary penalties, and if you read to the end, you will learn how to avoid them altogether. Yes, OSHA fines and citations can be avoided!
What is an OSHA Violation?
By definition, an OSHA violation occurs when a business doesn't follow the safety rules set by OSHA, and thereby fails to protect workers from hazards. These rules are there to prevent accidents and keep workers from getting hurt. When a company breaks these rules, it can lead to OSHA violations and fines. OSHA penalties are given to companies that don't stick to the safety standards. These fines can be hefty, depending on how serious the violation is. The idea is to encourage businesses to protect employees, keep their workplaces safe, and follow the rules to avoid these penalties.
OSHA Penalties, Fines, and Citations
After understanding what an OSHA violation is, it's crucial to dive into the specifics of OSHA penalties, fines, and citations. These terms are related but have distinct meanings in the world of workplace safety.
OSHA penalties are punishments given to companies that break safety rules. These can include OSHA fines, which are amounts of money the company must pay as a result of violating these rules. On the other hand, OSHA citations are official notices that a company has not followed specific safety standards. While citations point out what went wrong, fines are the financial consequences, and penalties can include both fines and other forms of punishment, like mandatory training or operational changes.
In 2023, these are the Top 10 Most Cited OSHA Violations for the General and Construction Industry. Check our updated article about these frequently cited standards for more details:
|
6 Types of OSHA Violations
OSHA identifies six types of violations, each varying in seriousness and, therefore, in the potential monetary penalties imposed. Understanding these categories is crucial for businesses to prioritize safety and avoid the costly consequences of non-compliance with OSHA standards.
1. Serious OSHA Violations
A serious violation is when a workplace hazard could endanger workers, either by illness or accident, that in all likelihood would cause serious injury or death - unless the owner or manager is not aware or could not have been made aware. To avoid this, it is best to do hazard identification and risk assessment to ensure workplace safety and avoid costly fines. The gravity of a violation is defined by the Gravity Based Penalty (GBP).
Gravity-Based Penalty (GBP)
A Gravity-Based Penalty (GBP) is a fine determined by the severity of an OSHA violation, reflecting how serious the breach of safety regulations is. The more severe the violation, the higher the penalty, aiming to motivate companies to maintain higher safety standards.
- High gravity violation - $16,550
Moderate gravity violation - $9,457 to $14,187
Low gravity violation - $7,093
This table shows the basis of GBP for serious violations. Severity + Probability = GBP.
Severity | Probability | GBP | Gravity | OIS/GRAVITY Code |
High | Greater |
$16,550 | High |
10 |
Medium |
Greater | $14,187 |
Moderate | 5 |
Low |
Greater | $11,823 |
Moderate | 5 |
High |
Lesser | $11,823 |
Moderate | 5 |
Medium |
Lesser | $9,457 |
Moderate | 5 |
Low | Lesser | $7,093 | Low | 1 |
2. Other-Than-Serious OSHA Violations
Other-Than-Serious violation is when a threat jeopardizes a worker’s occupational safety and health but does not end in injury or death. This has the same maximum penalty as a serious violation, but OSHA has the discretion to issue a citation or reduce the fine by 95%.
There are two classifications for other-than-serious violations. One is the lesser minimal-only violation, and the other is the greater minimal-only violation. The distinction between these two lies in the potential impact of the hazard. Lesser minimal-only violations are those where the risk to employee safety or health is considered low, leading to smaller fines.
On the other hand, greater minimal-only violations involve risks that, while still not life-threatening or likely to cause serious injury, are significant enough to warrant a higher penalty compared to lesser minimal-only cases.
3. Willful or Repeated OSHA Violations
Willful or repeated willful violations are the most severe. A violation is willful when the owner or manager, being informed of a hazard, refuses to fix it or acts apathetic to worker safety, as well as OSHA regulations. This is also called purposeful disregard.
If a serious and/or willful violation of rules is repeated within 3 years, the company at fault will incur devastating fines. Below is the 2025 update on the Serious Willful Penalty Reductions based on the number of employees.
Employees | Percent reduction |
10 or fewer | 80 |
11-20 |
60 |
21-30 |
50 |
31-40 |
40 |
41-50 |
30 |
51-100 |
20 |
101-250 |
10 |
251 or more | 0 |
4. Posting Requirements OSHA Violations
Once the business receives the OSHA notice, the employer must post it (original or copy) at or near the incident area. Doing so is part of OSHA requirements to alert the employees of the hazards. The said notice is to be kept posted for 3 working days (excluding weekends and Federal holidays) or until the hazard is abated, whichever is longer. Read more about the OSHA recordkeeping and reporting requirements here.
The employer can choose from either of these options:
- Resolve the condition by the date specified in the OSHA notice
- Request an Informal Conference within 15 working days
5. Failure to Abate OSHA Violations
Failure to abate is incurred when a business owner fails to resolve their own safety and health administration violation within the date set in the OSHA Notice. The said violation is then subject to the maximum penalty per day past the abatement date.
6. De Minimis Violation
De minimis is a Latin phrase that can be translated as “about minimal things.” Hence, it is defined as lacking significance or importance - something so minor as to merit disregard. An act of OSHA de minimis is a violation with no direct or immediate relationship to safety or health. This violation type does not lead to penalties or citations.
For example in ladder safety requirements, OSHA requires a 12-inch distance between ladder rungs, so a 13-inch space is non-compliant, but a citation or notice may not be needed.
OSHA Fines: Minimum - Maximum per Violation
Understanding the range of OSHA fines for different types of OSHA violations is crucial for businesses aiming to comply with safety regulations. These fines are set within a minimum and maximum range, reflecting the severity and nature of the violation. Knowing these limits helps companies gauge the potential financial impact of safety oversights and prioritize corrective actions.
Type of Violation | Minimum Penalty | Maximum Penalty |
Serious | $1,221** |
$16,550 |
Other-Than-Serious |
$0 |
$16,550 |
Willful or Repeated |
$11,823* |
$165,514 |
Posting Requirements |
$0 |
$16,550 |
Failure to Abate | N/A | $16,550 per day unabated beyond the abatement date (generally limited to 30 days maximum) |
* For a repeated other-than-serious violation that otherwise would have no initial penalty, a GBP penalty of $472 shall be proposed for the first repeated violation, $1,182 for the second repeated violation, and $2,364 for a third repetition.
**This amount reflects the actual minimum penalty with all penalty reductions which rectifies error in the previous years' serious minimum penalty posted.
You may visit their website if you’re interested in checking for OSHA enforcement inspections by the name of the establishment.
What is the best technique to avoid OSHA penalties and fines?
In a word, avoiding OSHA penalties and fines is avoiding violations.
The most efficient way to achieve this is by creating a safe working environment for every employee's health and safety. To do this, you need to identify and then resolve all identified potential hazards in your workplace. Your employees should be trained on proper safety procedures for their daily operations and prepared in the event of emergencies.
The following steps are recommended by OSHA to employers and workers in identifying and assessing workplace hazards:
- Collecting and reviewing data that show existing hazards or any possible risks in the workplace.
- Conducting diagnostic and regular workplace safety assessments to pin down both new and recurring risks.
- Investigating injuries, illnesses, accidents, and incidents to detect the causal hazards and address the weak points of the safety and health program being utilized.
- Categorizing related accidents and determining patterns in injuries, illnesses, and documented hazards.
- Considering threats associated with emergency or unusual cases.
- Determining the gravity and possibility of accidents that could result in any of the identified hazards and making this data the basis for prioritizing corrective and preventive actions.
Check out these OSHA-recommended practices in preventing and controlling workplace hazards:
- Action item 1: Determining control options
- Action item 2: Choosing appropriate controls
- Action item 3: Establishing and updating a hazard control program
- Action item 4: Choosing appropriate controls to ensure workers’ safety during emergencies and nonroutine cases
- Action item 5: Implementing chosen controls in the workplace
- Action item 6: Following up to validate the effectiveness and efficiency of chosen controls
Awareness of OSHA violations will help business owners become more adherent to the guidelines and requirements for employee safety set by OSHA. Avoiding these violations means safety for the workers and steering clear of costly OSHA penalties and fines.
OSHA Violations FAQs
What are the top 5 OSHA violations?
The top 5 OSHA violations typically include:
Inadequate fall protection
- Failure to communicate hazards
- Unsafe scaffolding
- Lack of respiratory protection
- Improper control of hazardous energy (lockout/tagout).
How much is the OSHA penalty?
The OSHA penalty amounts for 2025 have been adjusted for inflation. The maximum penalties for serious and other-than-serious violations are now $16,550 per violation. For willful or repeated violations, the maximum penalty has increased to $165,514 per violation.
What is the biggest OSHA fine?
The biggest OSHA fine can exceed $1 million, especially for willful or repeated violations involving severe risks or fatalities.
What qualifies as an OSHA violation?
An OSHA violation occurs when an employer does not comply with OSHA's safety and health standards, leading to unsafe working conditions that could harm employees.
What is the penalty for lying to OSHA?
Lying to OSHA, such as providing false information during an investigation, can lead to criminal charges, with penalties including fines and imprisonment.