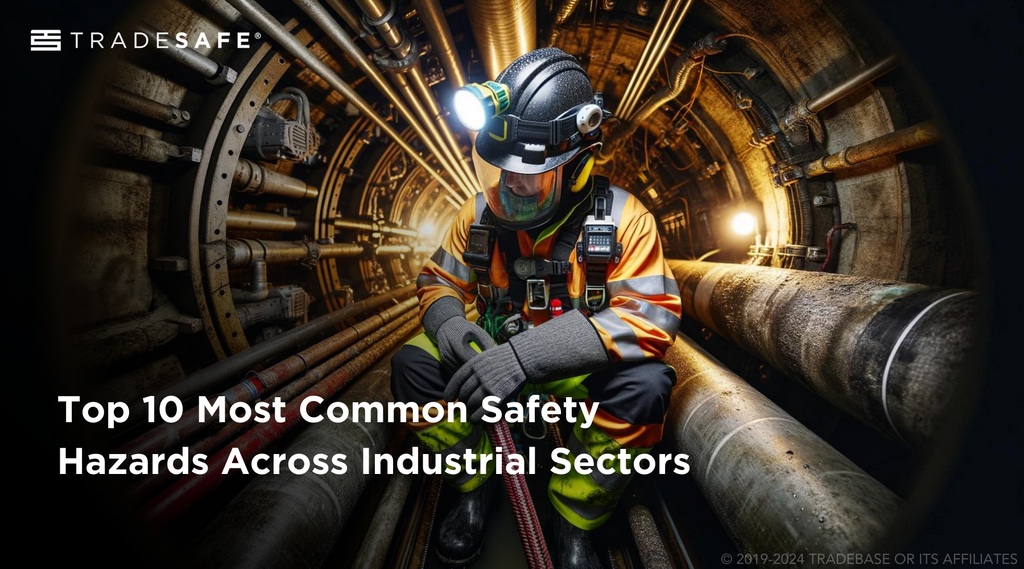
I have been working in the occupational health and safety field for thirteen years, and initially, my concept of workplace safety hazards conjured images of large equipment, huge machines, and explosive operations. However, as I've gained experience, I've come to realize that the most common injuries often result from smaller, easily overlooked risks. It’s the little things, as they say—the devil is in the details. While enormous hazards undoubtedly command attention and are universally recognized, it’s typically the subtle, seemingly insignificant hazards that lead to the most injuries. These smaller risks are pervasive, crossing industry boundaries and appearing in nearly every workplace. Although large equipment and manual labor risks often feature on Top 10 Hazard Lists, it's the less obvious hazards that might surprise you with their potential for harm.
What is a Workplace Hazard?
According to the Occupational Safety and Health Administration (OSHA), a workplace hazard is any source of potential injury, harm, or adverse health effect on a person or environment in the workplace. OSHA categorizes these hazards into various groups, including safety, biological, chemical, ergonomic, physical, and psychological hazards. The organization underscores the necessity for employers to assess their working environment to identify and mitigate potential hazards, thereby preventing injuries and illnesses. OSHA also supports this process by offering guidelines and resources aimed at helping both employers and employees recognize and effectively manage these risks.
What is a Hazard Identification Procedure?
Hazard identification procedures are the foundation for building a proactive safety culture. They transform workplaces from reactive to preventative by systematically searching for hidden hazards. This procedure involves scrutinizing the working environment to detect any conditions, activities, or factors that could potentially cause harm, be it physical injury, health impairment, or significant disruption in operations.
The effectiveness of a hazard identification procedure hinges largely on the thoroughness with which the workplace is examined and the level of employee engagement in the process. A comprehensive approach includes examining past incident reports, near misses, and routine operations to pinpoint where risks might emerge. It also integrates insights from employees who, through their daily tasks, may notice subtle changes or potential dangers not immediately obvious to safety officers or management. This collective vigilance ensures a broad perspective on safety, enhancing the detection and mitigation of risks.
Importance of Identifying Workplace Hazards
Understanding the various types of hazards in the workplace is crucial for several reasons. It not only helps in maintaining a safe environment but also contributes to the overall well-being and efficiency of the employees. Here’s why it’s so important:
- Employee Empowerment: Knowing about the different types of hazards in the workplace empowers us as employees. When we know what to look out for, we can better avoid risks and maintain workplace safety.
- Reduced Accidents and Costs: Preventing accidents isn't just about avoiding injuries; it also saves money. Fewer accidents mean less downtime and lower costs from medical bills and insurance. It's a win-win for both employers and employees.
- Improved Work Environment: Focusing on safety helps create a positive work environment. When employees feel safe, they are more satisfied and productive. Occupational safety isn't just about following rules—it's about building a culture where everyone looks out for each other.
Top 10 Workplace Safety Hazards
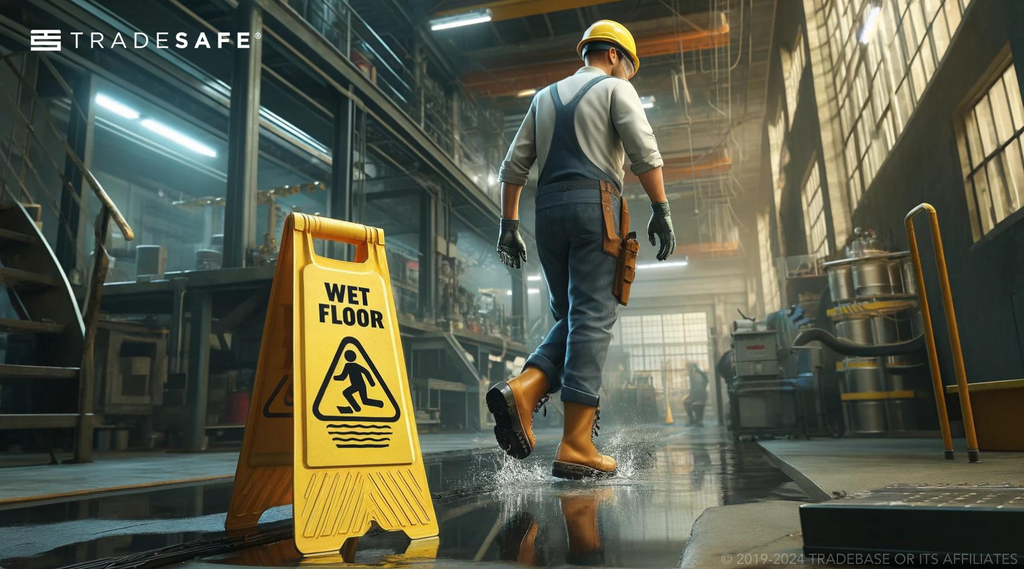
Slips, Trips, and Falls
Slips, trips, and falls (at the same level) can happen anywhere and may occur individually or all three can happen within the same incident. Slips are most often due to slippery substances or materials on the floor or shoes, or due to a change in the type of flooring from room to room. Trips most often occur due to obstructions in walking areas, unsecured cords in rooms, or uneven floors or walking surfaces. Falls at the same level happen usually due to a slip or trip where an employee is unable to correct their balance.
This safety hazard can happen at any workplace regardless of the sector, from heavy industrial sites to offices, and can lead to a range of injuries, from minor bruises and sprains to more severe consequences like fractures, head injuries, or even fatalities. To prevent these accidents, it is essential to maintain clean and organized workspaces, use non-slip mats in slippery areas, ensure adequate lighting, and keep areas such as emergency exits clear. Regular inspection and maintenance of flooring can also significantly reduce or eliminate the risk.
Fire Hazards
Fire hazards in the workplace typically stem from improper storage of flammable materials, faulty electrical equipment, or insufficient fire safety measures. The consequences of workplace fire hazards can be devastating, resulting in severe burns, respiratory injuries from smoke inhalation, and significant property damage. It is crucial to safely store all combustible materials, regularly maintain electrical systems, keep working areas and fire emergency exits clear, and all fire safety equipment like extinguishers are accessible and in good working order. An essential part of fire safety is clear, visible workplace safety signs to easily indicate the location of fire extinguishers.
Manual Material Handling
Manual material handling is most often thought of as large loads where employees are working in warehouses or at the docks in more industrial settings. While these settings most definitely qualify as encountering material handling hazards, there are some manual material handling that happens in every workplace, across all sectors.
People who work in smaller shops contend with material handling in the form of parts, boxes of odds and ends, middling to heavy tools, and moving storage items around. Even workers in office jobs around an industrial site often encounter material handling daily in their workplace tasks. Carrying reams of blank paper for photocopy machines, shifting desks and filing cabinets, and carrying multiple large binders are all part of material handling.
Managing material handling hazards can take the form of teaching workers correct material storage and handling postures, using trolleys, and encouraging workers to use tandem lifts when items are too heavy for one person and mechanical means are not available.
Workplace Violence
In 2020, service occupations accounted for about half of all nonfatal intentional injuries by another person that required at least a day away from work. These behaviors can range from supervisors using intimidation tactics to "teach a lesson" to subordinates, to physical assaults, and even homicide. Harassment may also manifest as ongoing unwelcome behaviors, whether sexual or otherwise, targeted at individuals. Both violence and harassment in the workplace are legally unacceptable and defined as any threats of violence, actual acts of violence, intimidation, insults, belittling, sabotage, blocking promotions, and more, occurring within the work environment.
Implementing a no-tolerance violence and harassment policy and training all levels of workers in the identification and prevention of violence and harassment is the best way to ensure employee safety. It is important to ensure that a whistleblower protection policy is implemented as well, to ensure personnel who report violence incidents and harassment are protected from adverse repercussions.
Chemical Toxic Substances
Chemicals are common in work areas, whether used in the product manufacturing industry or for cleaning and maintenance tasks. The risks associated with exposure to these hazardous materials vary depending on their nature and the environment in which they are used. In industrial settings, for instance, the chemicals might be highly corrosive or toxic, utilized in the manufacturing or treatment processes.
Regardless of the setting or purpose, all chemicals and other hazardous materials must be handled with caution and safety. Employers must ensure safety by providing employees with several key resources: the Material Safety Data Sheet (MSDS) for each chemical, appropriate personal protective equipment (PPE), and training. This training should cover how to effectively understand and use the MSDS, chemical products' safe handling, and the correct use of the necessary PPE.
Mechanical Hazards
Mechanical hazards are prevalent in work areas that use heavy machinery and tools. These hazards typically arise from moving parts, sharp edges, or hot surfaces that can easily cause injuries. Employees might face severe risks such as cuts, lacerations, amputations, burns, or even crushing injuries from interacting with these mechanical systems. To mitigate these risks, it is essential to maintain all heavy machinery and tools properly and use them only for their intended purpose, ensure that safety guards are in place, provide comprehensive training on emergency and safe operation practices, and enforce workers to wear appropriate personal protective equipment (PPE).
Working at Heights
Working at heights refers to any work activity where the worker can face a fall of 3 feet (1m) or higher in walkway areas or 9 feet (3m) or higher on scaffolding, ladders, and roofs. This includes work in areas such as loading docks, using scissor lifts and other aerial platforms, or holes in the work area floor. The consequences of such falls can be severe, ranging from serious injuries to fatalities, with additional hazards such as dropped objects causing injury to others below.
Prevention strategies, especially in construction, should include using fall protection systems like harnesses, guardrails, and safety nets. When a fall hazard is present along a walkway, it is recommended to install guardrails to prevent workers from falling. Additionally, if the potential fall is from a height of 9 feet or more, fall protection safety equipment and systems are required to ensure worker safety. Employees must receive proper training on the correct setup and safe use of this equipment, and all gear should be regularly inspected to ensure it is safe for use.
When any working at heights tasks must be completed the following protective mechanisms should be in place:
- Permit system
- Emergency response plan
- Fall protection plan
- Barricades
- Inspection tag usage for ladders scaffolds and other equipment used in the process
- Safe work procedure
- Only trained workers complete work at heights
Electrical Risks
Electrical hazards in the workplace can lead to serious accidents, including electrocution, electric shocks, arc flashes, and fires or explosions. Electrocution, often fatal, occurs when a worker comes into direct contact with live wires or highly energized equipment. Electric shocks, which can range from mild tingles to severe burns and cardiac arrest, typically result from improper handling of power tools or defective equipment. Arc flashes, explosion of energy from electrical arcs, can cause severe burns and blindness, often occurring during short circuits or improper servicing of equipment.
To prevent such incidents, it's crucial to inspect electrical equipment and wiring regularly, adhere to proper lockout/tagout procedures, and ensure all personnel are well-trained in electrical workplace safety and emergency. Additionally, appropriate personal protective safety equipment should be used, and conductive materials must be kept away from electrical sources.
Working Alone
When an employee is working alone, their vulnerability can increase significantly in situations where they are isolated from communication devices or unable to use their communication device. This isolation can complicate timely assistance in case of emergencies. The risks when working alone can include:
- Slips, trips, and falls
- Injuries from tools and equipment
- Violence and harassment with no backup around
All other common incidents are magnified by isolation and the possibility that communication is not possible. Organizations should implement a working-alone emergency communications policy to ensure that employees who fail to report or check in are missed and aid is dispatched. Identify the possible hazards and risks an employee will face while working alone depending on the tasks and area the employee is working in, develop a communications procedure for each case, and train employees to effectively implement and use the working alone procedure.
Confined Spaces
Confined spaces are work areas with limited entry and exit points, not designed for continuous occupancy, such as tanks, silos, and tunnels. The restricted nature of these spaces increases the risk of serious hazards including asphyxiation, poisoning, and explosions, and can complicate rescue efforts in emergencies. To enhance workplace safety, employers must undertake comprehensive measures, which include conducting risk assessments to identify potential dangers, ensuring that the spaces are well-ventilated to prevent hazardous atmosphere buildup, and continuously monitoring air quality.
Additionally, all employees should receive thorough training on the risks associated with confined spaces and the necessary occupational safety protocols. Organizations must also establish and rehearse confined space emergency response procedures and ensure that workers have the appropriate personal protective safety equipment, such as respirators and gas detectors.
Complacency
An often overlooked element when identifying hazards is the complacency that happens when personnel become adept and efficient at their jobs. They can begin to complete tasks automatically without actively thinking about hazard identification and control. Complacency can also come into play when nothing bad has happened or almost happened.
Without even being aware or realizing it, employees can start to believe that since they have never been injured or had an incident they won’t. This is when elementary safety precautions such as gloves, safety glasses, locking devices, and machine and tool guards are removed. Employers can use a variety of tools including safety or toolbox talks, inspections, and a buddy system where teams of employees work together to hold each other accountable for working safely.
Best Safe Work Practices to Maintain Industrial Workplace Safety
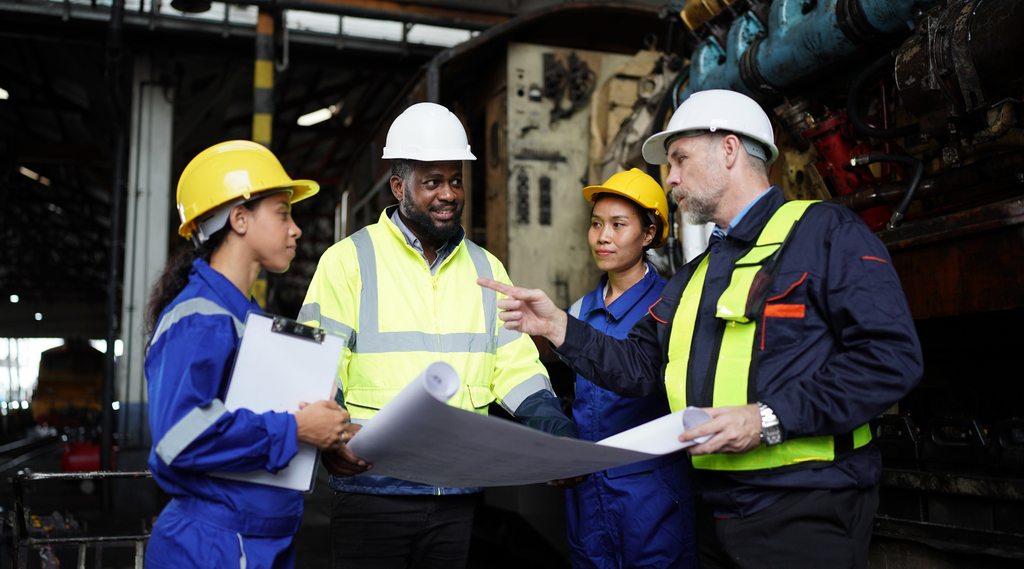
While adhering to occupational safety regulations is crucial, workplace safety and productivity thrives on a culture that goes beyond mere compliance. Here, we take a closer look into the key components that foster a strong safety culture, empowering your workforce to protect themselves and minimizing risks:
Cultivating a Safety Mindset
Imagine a workplace where safety isn't an afterthought, but an ingrained value. This proactive approach requires shifting focus from simply reacting to accidents to preventing them altogether. Empower employees to become active participants in safety. Encourage them to report near misses, identify and report hazards, and even have the authority to halt unsafe work practices. By fostering a culture of open communication and shared responsibility, you create a safety net far stronger than health and safety regulations alone.
Leveraging Technology for Enhanced Safety
Modern technology offers a treasure trove of tools to further productivity and bolster safety measures. Predictive maintenance, for instance, utilizes sensors and data analysis to anticipate equipment failures before they occur, preventing accidents caused by malfunctioning machinery. Virtual Reality training allows workers to practice safe procedures in a controlled, immersive environment, particularly valuable for high-risk tasks. By embracing these innovations, you equip your workforce with the knowledge and skills to navigate potential hazards with confidence.
Prioritizing A Holistic Approach to Safety
A safe work environment goes beyond physical security. Recognizing the connection between mental health and physical well-being is crucial to keeping people safe too. Fatigue management strategies, such as well-designed shift schedules and designated rest areas, can significantly reduce accidents caused by worker exhaustion. Furthermore, addressing mental health through programs that tackle stress, anxiety, and depression fosters focused and resilient workers, less susceptible to workplace safety lapses.
Leading Data-Driven Decisions
Traditionally, occupational safety programs focus on lagging indicators - accidents that have already happened. However, a truly proactive approach emphasizes leading indicators. These are quantifiable measures like near misses, workplace safety violations, and unsafe work practices. By tracking and analyzing leading indicators, you can identify trends and intervene before incidents occur. Investing in safety analytics allows you to pinpoint areas with high risks and tailor preventative measures accordingly. Data empowers you to move from reactive to predictive, safeguarding your workforce from potential dangers.
FAQs on Industrial Hazards
What is the biggest safety hazard in the workplace?
The biggest safety hazard can vary by industry, but generally, slip and fall accidents rank highly across all sectors.
What are the four categories of hazards from OSHA?
OSHA categorizes workplace hazards into four groups: physical, chemical, biological, and ergonomic.
Do all hazards require a pictogram?
Not all hazards require a pictogram. OSHA requires pictograms for chemical hazards as part of the Globally Harmonized System (GHS).
What is a hidden hazard?
A hidden hazard is a risk that is not immediately obvious but can cause harm if not addressed, such as stress or ergonomic issues.
How do you identify a hazard?
Identifying a hazard typically involves a combination of visual inspections, reviewing safety data, and gathering employee feedback.