LOTO Kits, Locks, Tags, Devices, and Supplies
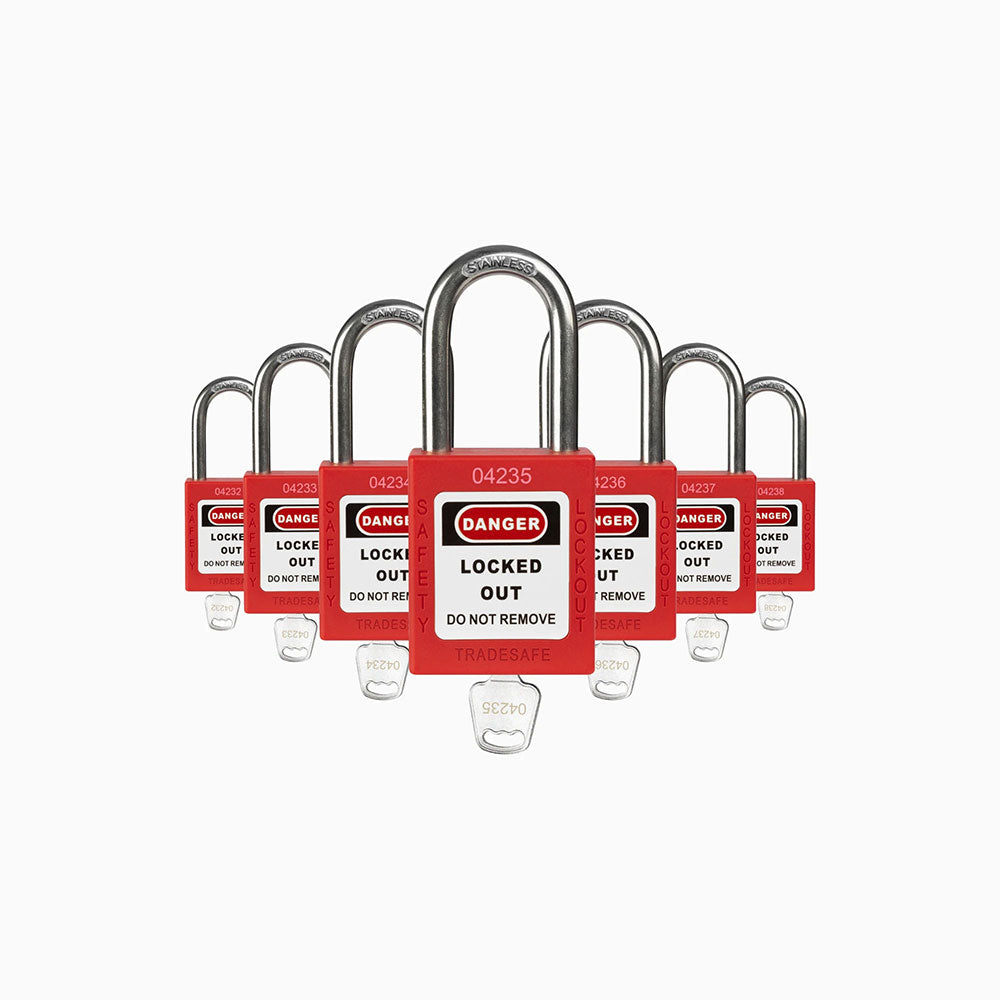
Lockout Tagout Locks
TRADESAFE’s lockout tagout locks are premium quality, guaranteed to be durable, corrosion-resistant, and – most importantly – compliant with OSHA 1910.147. These aren’t your ordinary hardware store padlocks. They are specially designed for lockout tagout applications and are made to be able to keep up with the demands of industrial facilities.
Keyed alike and keyed different locks are available. Locks can also come with one key or two keys. All keys are engraved with a set of numbers that match the numbers on their corresponding lock. The locks also have a key-retaining feature, which means that they won’t release their keys until they’re securely locked. This helps provide an extra level of security and safety.
These padlocks are highly versatile and can be used in a variety of ways. Because of their hardwearing construction, they can withstand heavy and regular use.
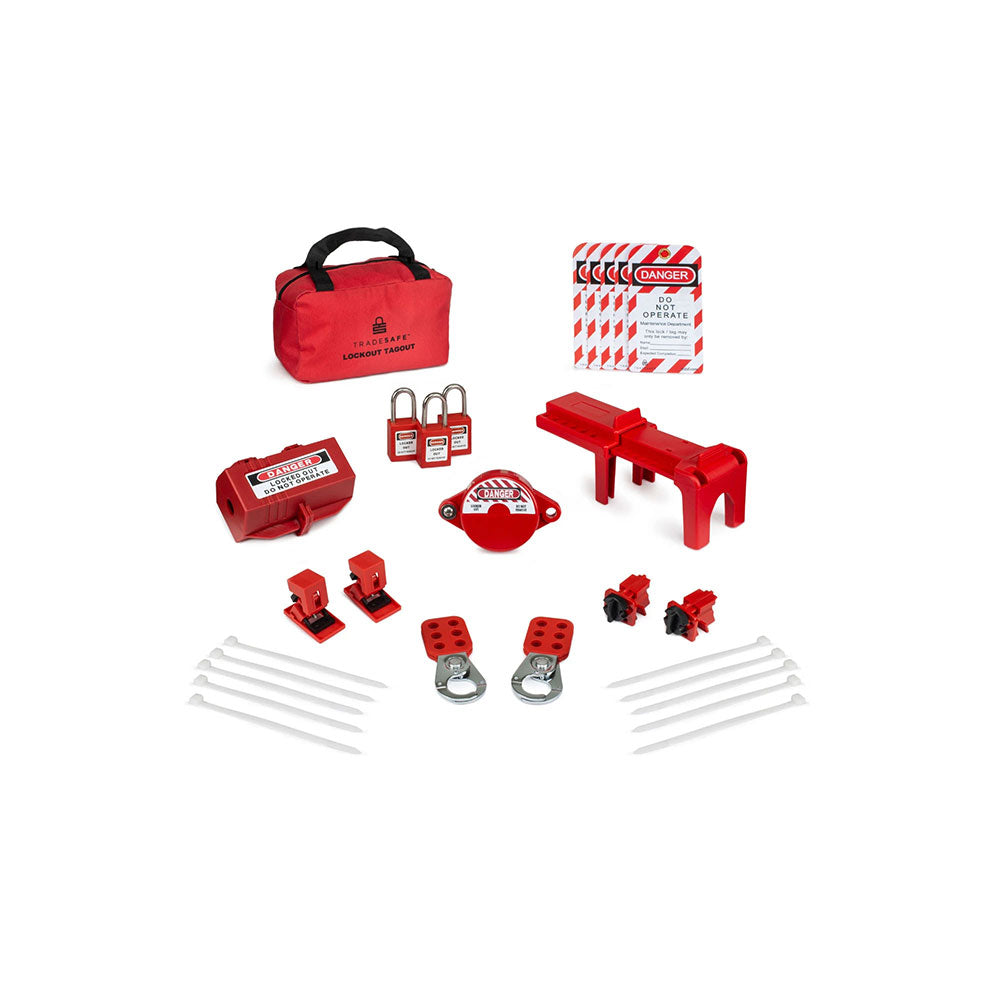
Lockout Tagout Kits
A grouping of Lockout Tagout devices sold in kits meant to be used individually or to refill safety stations. Our Lockout Tagout Kits are each assembled with a different grouping which may include hasps, safety padlocks, do not operate tags, electric circuit breaker lockouts, electric plug lockouts, ball valve lockouts, gate valve lockouts, nylon attachment ties and other commonly used lockout devices that comply with OSHA 1910.147.
Our LOTO Kits, and the devices included, are designed and manufactured for durability, compliance, only of the finest materials, and with industry expert input throughout. All devices packed in a space saving vibrant red canvas carrying pouch with prominent Lockout Tagout printing to make identifying the kit easy.
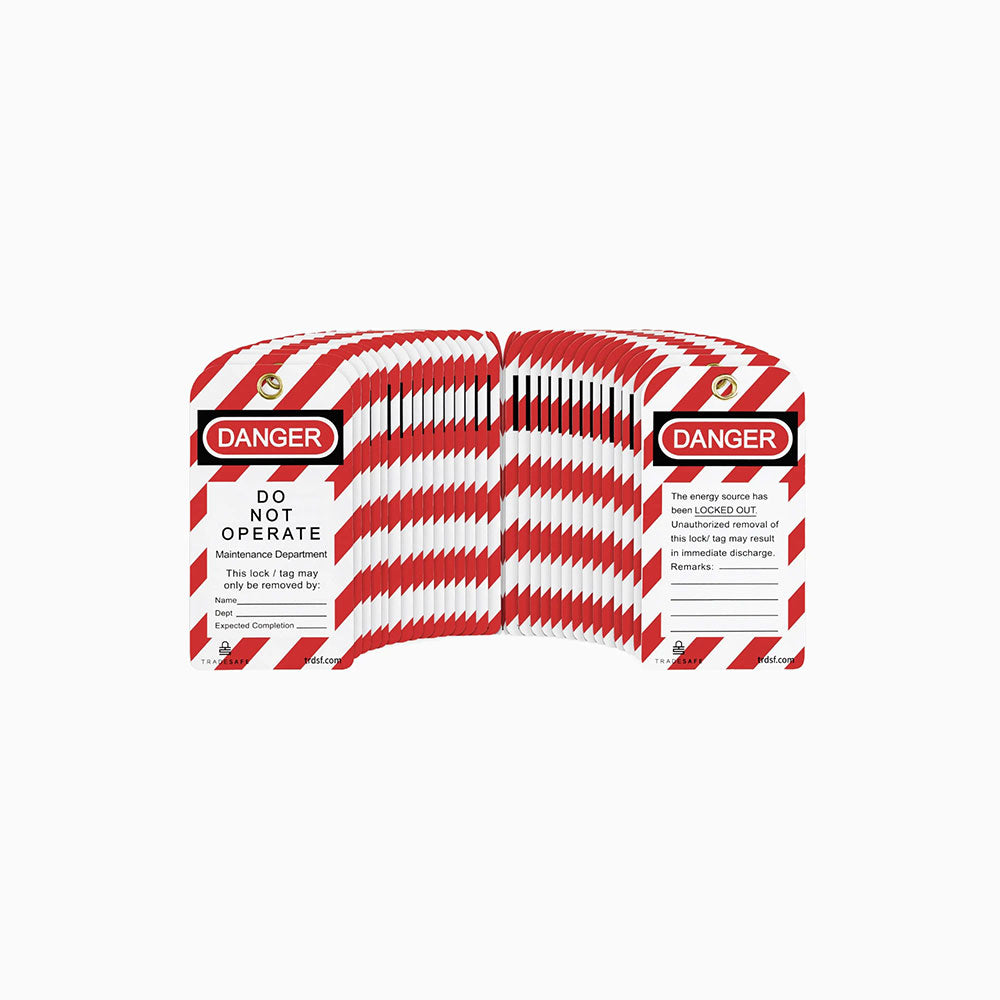
Lockout Tagout Tags
Durable, practical, and OSHA compliant Lockout Tags that properly warn against hazardous conditions and obviously alert that danger is present with a white, red, and black color scheme. Packed are 30 tear and moisture resistant, writable 15 mil nylon plastic LOTO tags measuring 5 1/2 inches x 2 inches with 1/3 inch diameter brass lined fastener hole. When using a marker to notate lockout details, these tags are able to maintain their functionality in extreme conditions. Some of the more notable OSHA compliant regulations that these tags meet include 1910.147(c)(5)(ii)(A)(3), 1910.147(c)(5)(iii), 910.147(c)(5)(ii)(A), 1910.147(c)(5)(ii)(C)(2). All our lockout tags come with an equivalent amount of 6 inch vinyl one piece all environment cable ties that are non-reusable, attachable by hand, self-locking, non-releasable, and maintain greater than 50 lbs of unlocking strength.
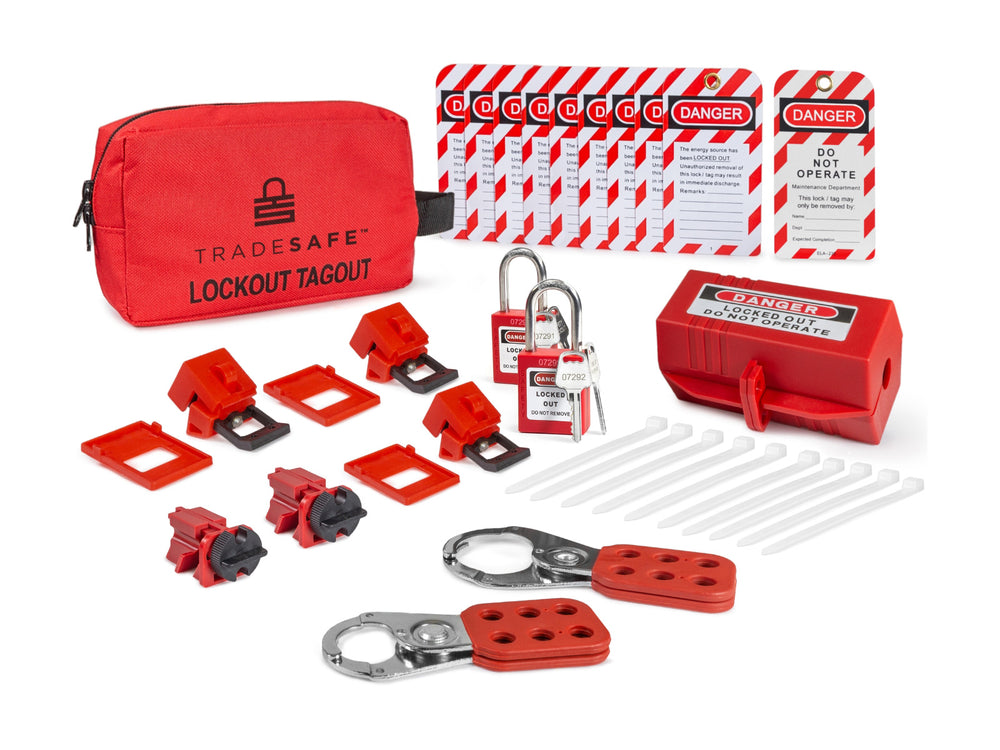
Lockout Tagout Electrical
Electrical hazards are some of the trickiest that workers face on a daily basis. Live wires with high voltages can’t be identified until they accidentally get touched, and with large power sources, there are no second chances.
Having the ability to lockout electrical connections makes it safe for workers to service machines while ensuring that they aren’t exposed to unnecessary risk.
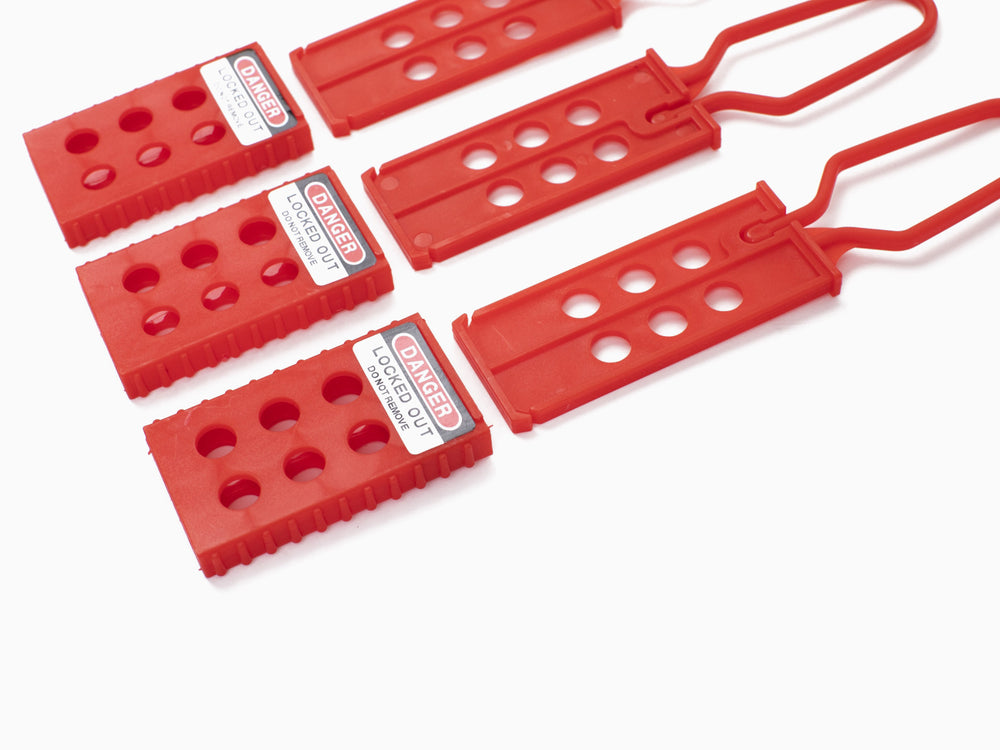
Lockout Tagout Hasps
Since most points of locking or lockout devices only have one place to use a lock, a hasp adds to the number of locks that can be used on one lockout point. Whether switching shifts, adding workers, or handing responsibility off to another crew, hasps allow the hazard to remain locked until all partied involved have approved its re-energizing and without shifting the responsibility of a lock to another competent person.
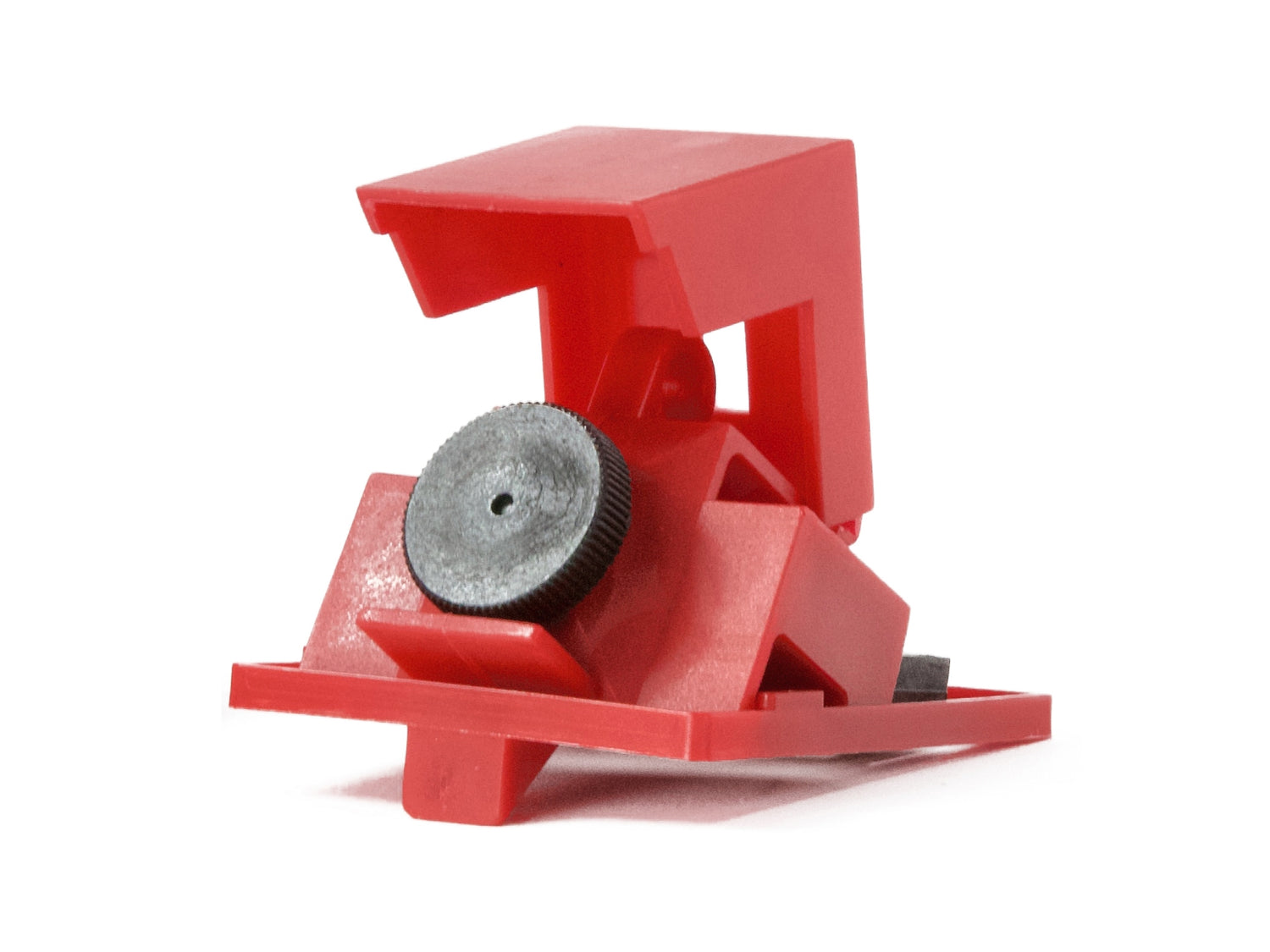
Lockout Tagout Breaker Locks
Keep maintenance personnel safe and workplace accidents nonexistent with the right lockout tagout circuit breaker locks. Quickly and efficiently secure breaker switches with these heavy-duty clamp-on locks. With TRADESAFE’s circuit breaker locks, you won’t have to worry about costly or dangerous mistakes. Because these locks are made of industrial-grade, non-conductive, and corrosion-resistant materials, they are guaranteed to be compliant with OSHA 1919.147. They are also easy to install and won’t require the use of screwdrivers or any other kinds of tools. These circuit breaker locks can easily secure single-pole breaker toggles that are 5/8 inch to 2.75 inches wide and 1/2 inch to 1 inch thick. A single lock can be used on different breakers of different sizes while maintaining safety for all workers involved.
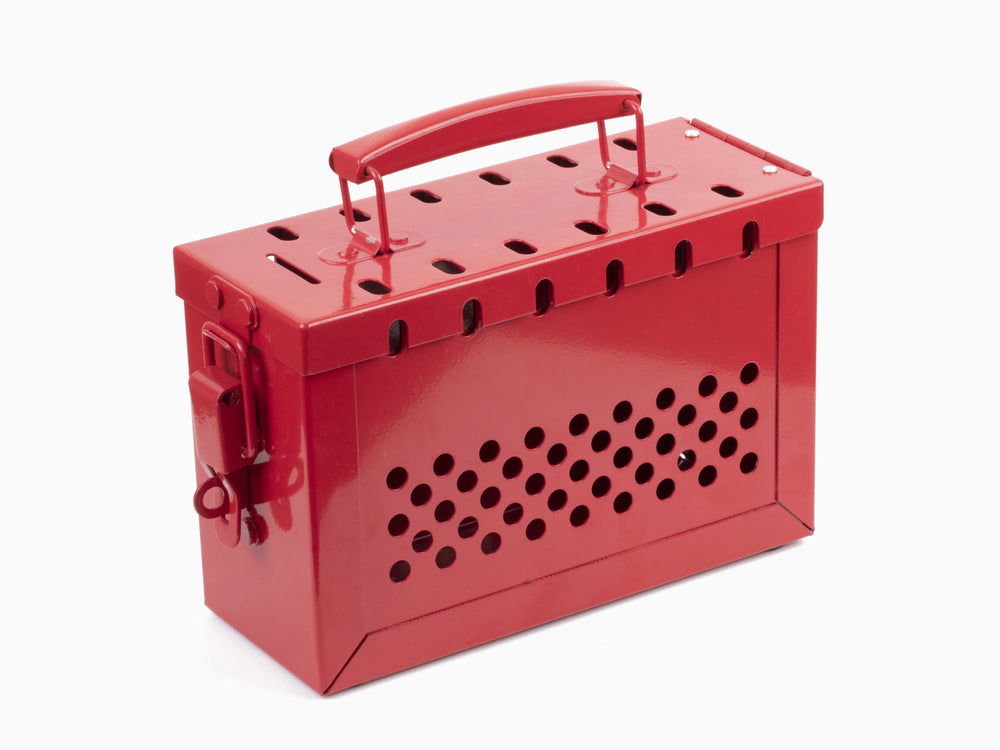
Lockout Tagout Lock Boxes
Lockout Boxes are an effective way for a group of workers to ensure that a power source or machine isn’t activated until everyone is ready. Each box comes equipped with rows of lock points, and adding a single padlock to any one of them completely prevents the box from being opened.
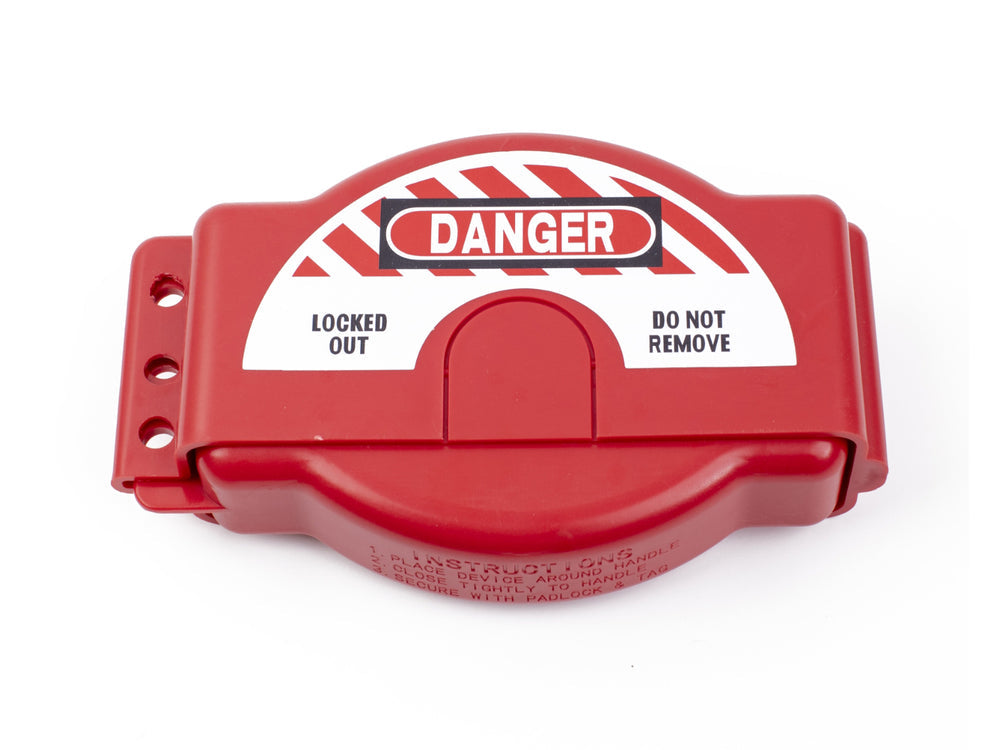
Lockout Tagout Valves
Isolating electrical energy isn’t the only hazard that needs to be worried about. Whether it’s the hydrostatic pressure in a pipe, or the mechanical energy stored in a spring, being able to effectively isolate that energy is the purpose of an effective Lockout Tagout safety program.
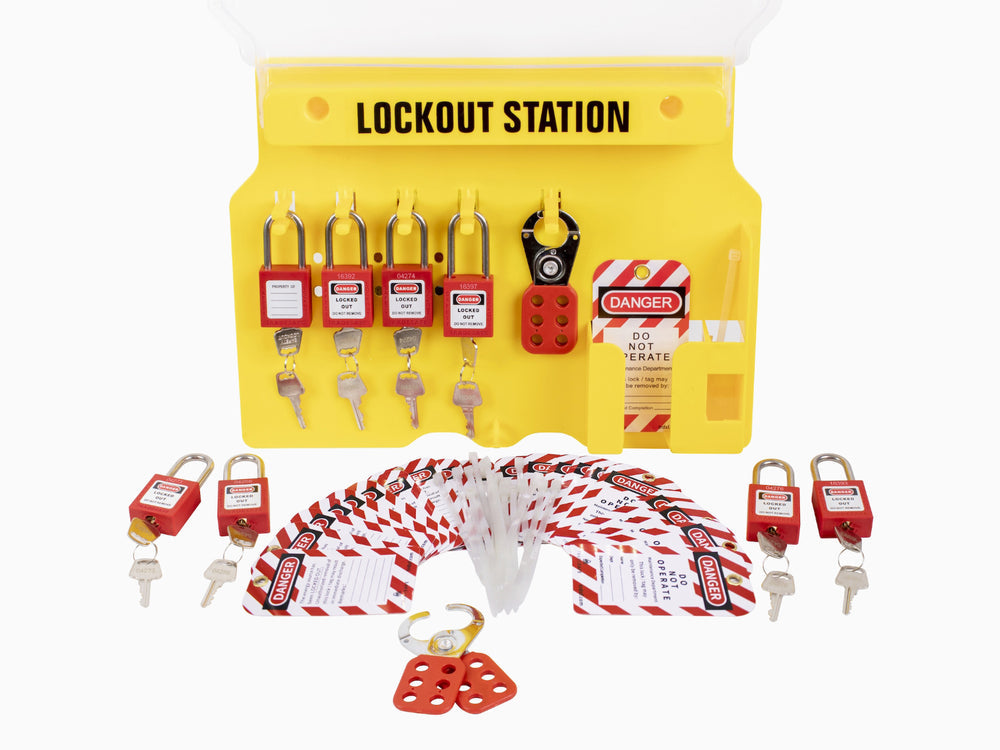
Lockout Tagout Stations
The only way that safety procedures are effective is if they are practiced every time. Unwilling workers will find any excuse they can find to avoid doing things by the book.
For places that regularly require Lockout Tag Out, having a dedicated Lockout Station eliminates the excuse that they don’t have the proper equipment. Keeping it close to where it’s most needed makes following LOTO procedures faster and easier. Emergencies are not the time to frantically search for locks.
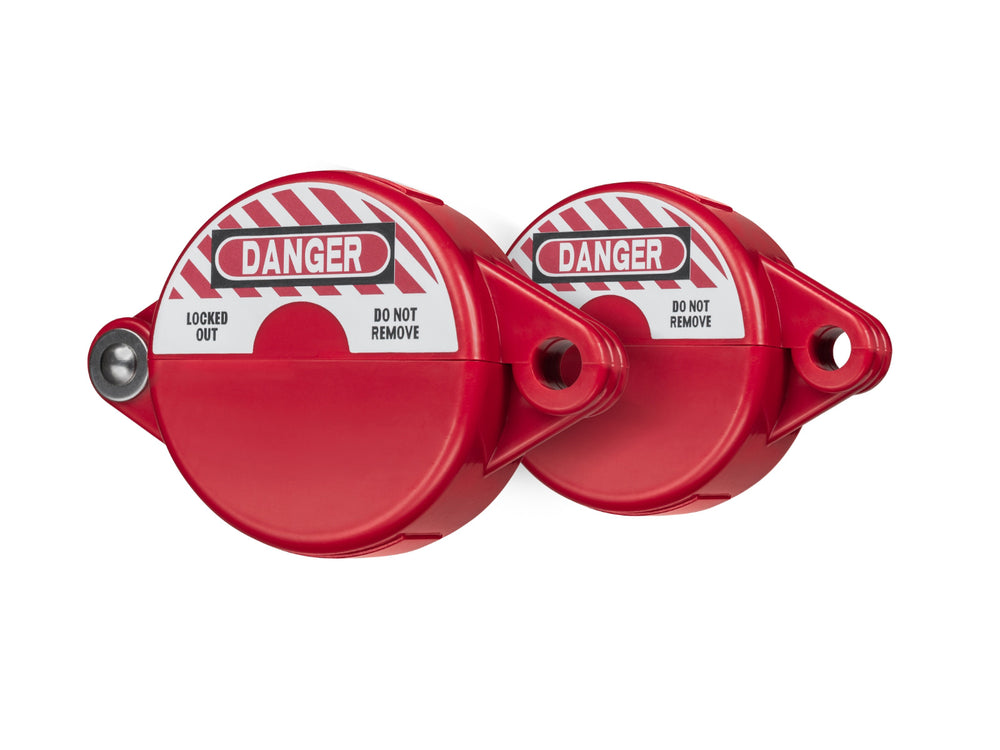
Other LOTO Devices
For all the other Lockout Tagout devices and supplies including hasps, ball valve lockouts, gate valve locks, electrical plug lockouts, electrical panel lockouts, lockout stations, group boxes, breaker lockouts, oversized lockouts for breakers, push button lockouts, cable lockout, cabinets, key knob lockouts, and more.
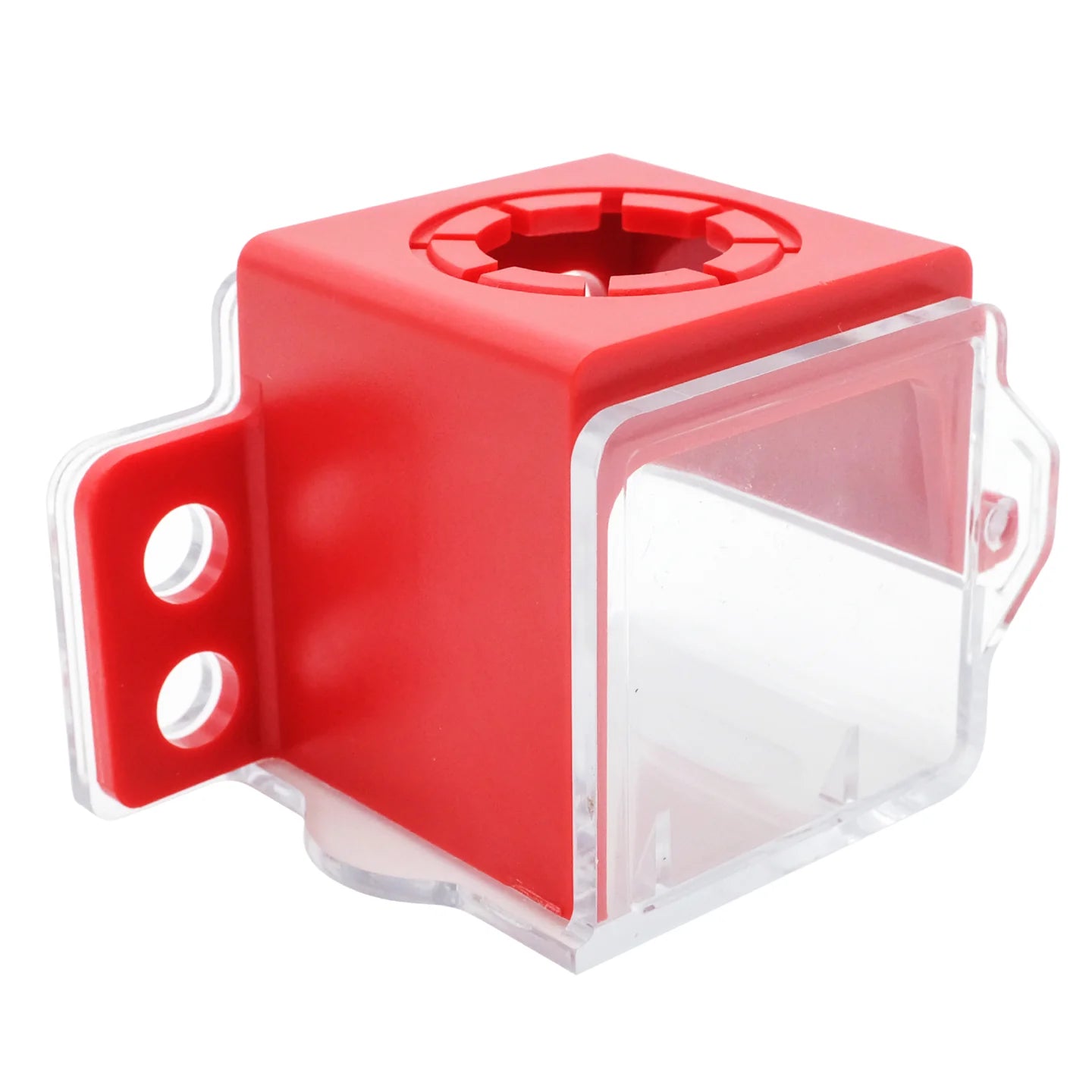
Lockout Tagout Push Button Cover
Machines are everywhere around us, especially in industrial workplaces. In order to start or stop machine operations, we use different types of control systems to do so. This is where push button switches are relevant. As the name suggests, a push button switch is an electrical device that relays the operator's pushing action to the machine. When it is pushed, the machine either starts or stops, depending on its state prior to pushing the switch. Different types of machines require specific design of push buttons. In line with this, push button lockout covers are designed to match the needs of industrial facilities dealing with various machineries. Oftentimes, push button lockouts are either round-shaped or box-typed and come in different sizes to accommodate varying push button switches.
TRADESAFE offers box-type push button lockouts from medium to extra-large size as well as round-shaped push button lockouts that is suitable for medium to large switches. These push button lockout covers are very easy to install using an adhesive tape or screw. There is also a padlock hole so the worker can attach a LOTO lock for added security.
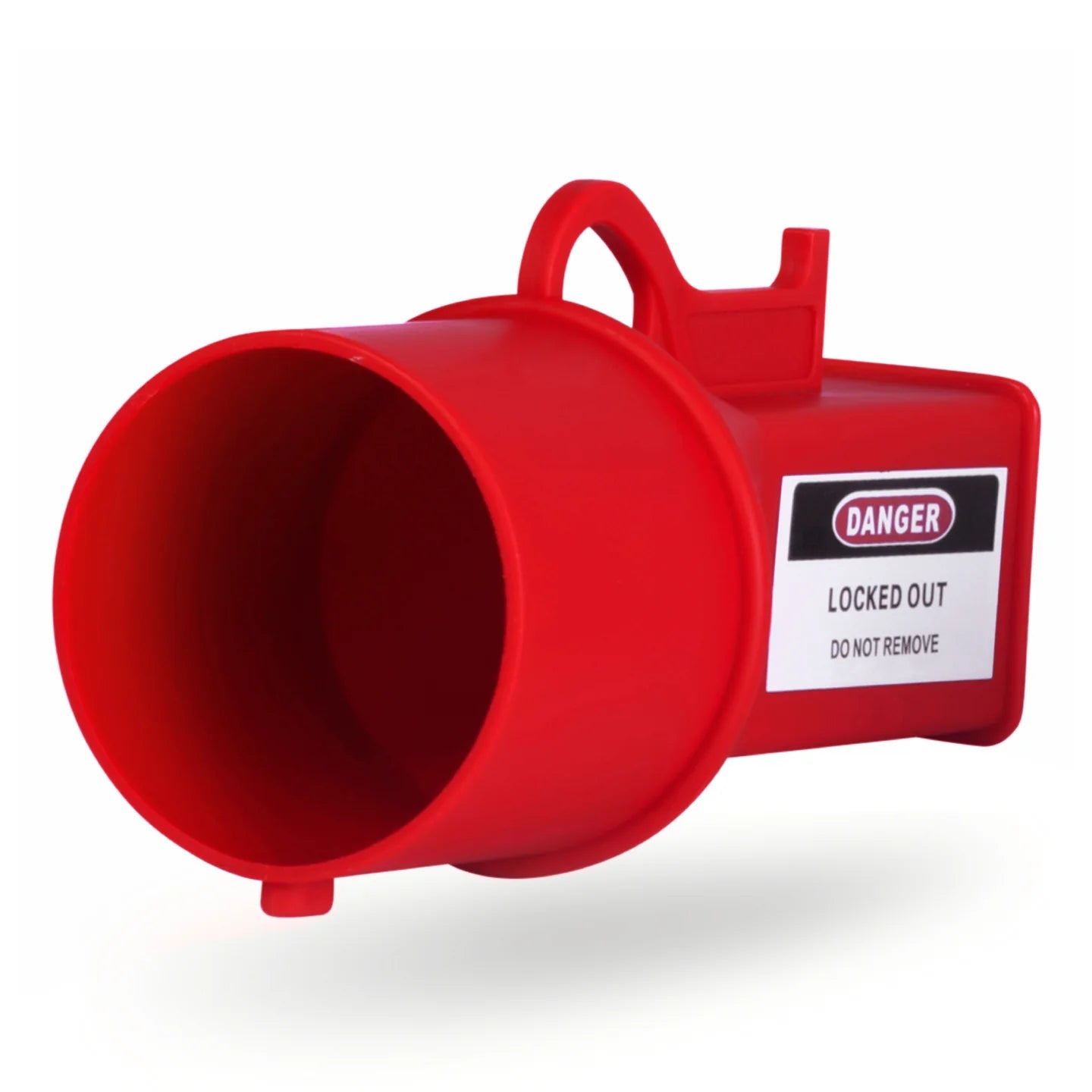
Lockout Tagout Pin and Sleeve Socket Locks
Pin and sleeve devices have become highly essential for heavy-duty industrial facilities that need to insulate power delivery from moisture, dirt, grime, and chemicals. There are five types of pin-and-sleeve devices, namely: plugs, connectors, receptacles, inlets, and mechanically interlocked receptacles.
As time went by, different variations of these devices are made, creating issues with compatibility and durability. This is where the International Electrotechnical Commission came in and set guidelines to standardize pin-and-sleeve devices.
IEC 309-compliant products meet global standards regardless of the manufacturer, thus ensuring compatibility between products.
Pin and sleeve devices are often the best choice for workplaces with power-hungry machineries and equipment. As such, they also pose serious risks to workers and industries using them. This is where pin and sleeve socket lockouts become significant. Any electrical device, no matter how durable it is guaranteed to be, will eventually undergo service, repair, or replacement. During these activities, following a lockout tagout procedure reduces the risk of unwanted workplace accidents by securely isolating energy-producing devices.
Pin and sleeve socket lockouts is a type of LOTO device especially designed for pin-and-sleeve devices. To ensure our safety partners only get the best precision-engineered lockout devices, TRADESAFE offers socket lockouts in its collection. With impact-resistant, bright red, plastic body, TRADESAFE pin-and-sleeve socket lockouts offer low conductivity, high visibility, and durability in heavy-industrial applications. Furthermore, these socket lockouts are guaranteed to be OSHA-compliant and easy to install. All the worker needs to do is lift the socket cover, insert the lockout device so it completely covers the socket, let the cover rest on top of the device, then attach a hasp and a LOTO padlock to securely keep it in place. These pin and sleeve socket lockouts can accommodate mini to large industrial sockets.
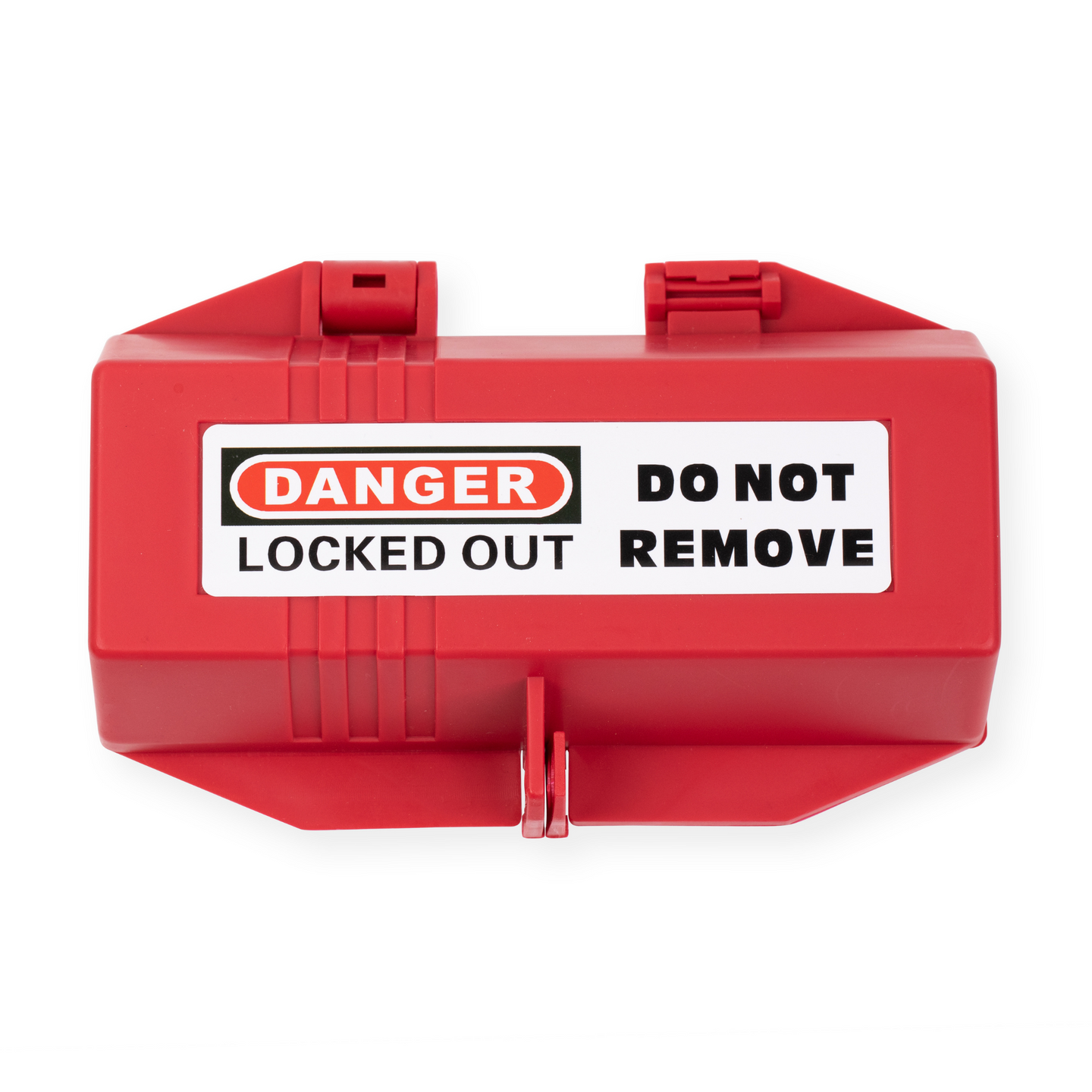
Lockout Tagout Supplies
A lockout tagout program can only be effective when it is coupled with appropriate lockout tagout supplies and devices. No matter how streamlined the LOTO program may seem, if the devices used in carrying out the procedures are substandard and do no meet OSHA requirements, workplace safety would still be jeopardized. TRADESAFE aims to not just be a LOTO supplier, but a trade partner. Our team is dedicated to be a one-stop shop for all industrial lockout tagout needs. With that being said, our collection ranges from LOTO padlocks, plug lockouts, breaker locks, valve lockouts, hasps, tags, and posters. Each lockout tagout device we offer are made from industrial-grade materials, engineered by expert professionals, and designed to be OSHA-compliant.
EXPLORE THE FULL TRADESAFE PRODUCT COLLECTION.
Lockout / Tagout FAQs
We are a USA headquartered and owned company and are focused on offering the very best quality and functionality of electrical and industrial lockout tagout sets, locks, kits, devices and supplies. We serve countless customers all across the country that day in and day out depend on our outstanding service, quality, functionality, and reliability. OSHA’s 1910.147 commonly referred to at Lockout Tagout federal regulations or Lock Out Tag Out (LO/TO) specifies safety requirements to include precautions and procedures to be implemented in relation to potentially hazardous stored energy sources. Examples of these could be circuit breakers, gas valves, equipment and machinery that could harm employees.
Developed with safety of workers of the highest priority, our LOTO devices are meant to be the primary tool in the compliance of these government regulations; in addition, they are equally important as for general workplace safety and play a pivotal role when part of any workplace safety program meant to protect the health and safety of all people potentially exposed to hazardous energy.
Here to not only serve your lockout tagout product needs, but also to provide useful resources that you can rely on to guide and improve your internal processes. Our Lockout Tag out Kits have been carefully thought out to make for a seamless restocking of stations, boxes, or even entirely new disbursements of equipment to employees or departments. We offer a wide variety of colors and key configurations of safety Padlocks, which come in 6 and 10 pack sets. This makes for a great opportunity to customize your lockout/tagout program based on specific needs. Do not operate lockout tags are increasingly important and instrumental in safe operations for almost any scenario where danger could be present. Our lockout Tags are we built and durable and come with the often overlooked, but extremely important, compliant attachments.