
Key Takeaways
-
Improper or missing safety tags can lead to severe injuries, legal consequences, and costly downtime due to unmarked hazards or equipment misuse.
-
OSHA requires specific tag types for various risks, with federal and state rules outlining when, where, and how to use them correctly.
-
Each tag type has a defined purpose and must be used properly to communicate risk and status.
-
Digital tools, such as QR codes, RFID tags, and mobile apps, improve accuracy, speed up inspections, and reduce tagging errors across worksites.
A technician I once worked with found a leak under a high-pressure steam valve. It wasn’t scheduled for repair, but he shut it off and flagged the issue. When he couldn’t find the proper danger tag, he used a scrap of cardboard and scribbled “Needs repair.” By the next shift, the valve looked fine on the outside, and the makeshift tag didn’t stand out. The crew pressurized the line, not realizing it had been isolated. Residual steam surged, and a worker was burned.
The isolation was the right move. The tag wasn’t.
This kind of thing happens more often than it should. Oftentimes, it points to poor training, rushed schedules, or a weak safety culture where clear safety signage in the workplace isn’t a priority. In some cases, supervisors or workers might not fully understand OSHA requirements, or they might think a shortcut will save time.
Slapping a tag on a serious hazard without considering whether it conveys the right message is like putting duct tape on a live wire. It might seem you’ve done something, but it’s not what keeps people safe.
OSHA Requirements for Safety Tag Use
The Occupational Safety and Health Administration (OSHA) mandates the use of a tagging system in specific situations and actively enforces proper implementation. Below are the key OSHA regulations that define how and when safety tags must be used:
-
-
29 CFR 1910.147 (The Control of Hazardous Energy): Requires employers to use lockout tagout tags during the servicing and maintenance of machines to communicate that energy sources are isolated and equipment must not be operated. The tags must be standardized, clearly worded (e.g., “Do Not Operate”).
-
29 CFR 1910.145 (Accident Prevention Signs and Tags for General Industry): Covers the general use of OSHA safety tags as hazard warnings. Tags must include a signal word such as “Danger” or “Caution,” and meet visibility and durability rules.
-
29 CFR 1926.200 (Accident Prevention Signs and Tags for Construction): Employers must use safety signage in the workplace to warn of hazards, with tag wording, design, and placement matching the standard.
-
Employers have a legal and ethical obligation to comply with these safety regulations to protect their workers. By using the appropriate safety tags, companies demonstrate their commitment to providing a safe working environment and reducing the potential for accidents and injuries.
State vs. Federal Variations
States with their own OSHA-approved plans may have stricter or updated standards. For example:
-
-
California (Cal/OSHA) often requires bilingual tags and tougher material standards.
-
Washington State mandates additional visibility tests for barricade tags near traffic zones.
-
Michigan requires additional documentation for lockout tagout tags during multi-contractor jobs.
-
Always check your state’s plan for tagging requirements, especially if you operate across multiple states or industries. Relying solely on federal rules can leave you exposed to violations, fines, and liability.
The True Cost of Misusing Safety Tags
Misusing safety tags can be just as dangerous and costly as not using them at all. These tags are designed to clearly and consistently communicate real hazards. When they're used the wrong way, ignored, or treated casually, the consequences can be serious. Here’s what the misuse of safety tags can cost your company:
Cost |
Description |
Injuries and Fatalities |
When a tag is missing, unclear, or used incorrectly, workers may unknowingly use a ladder that failed inspection; walk on a scaffold that isn’t secure; enter an area that’s still under repair; or operate a machine past its inspection window. This increases the risk of serious injury, exposure to hazardous materials, or tool malfunctions. |
False Sense of Safety |
Improper use of tags can send the wrong message. For example, using an outdated inspection tag may falsely signal that equipment is safe. Similarly, handwritten, unclear, or makeshift tags don’t give workers confidence or clear direction. |
Regulatory Fines and Compliance Failures |
OSHA and state agencies require proper tagging for many safety areas. Incorrect tagging or lack of standardization can lead to violations and fines, especially if an incident occurs. |
Delays and Downtime |
Misused tags often cause confusion. For instance, a machine might sit idle waiting for an unclear tag to be verified, or a scaffold with a tag that doesn’t match protocol may need to be re-inspected, wasting hours. |
Liability and Insurance Consequences |
If an incident occurs and it's found that the wrong type of tag was used or the tag wasn't updated properly, liability shifts back to the company. In legal investigations, improper tagging can be viewed as negligence. |
Guide to Safety Tag Types
Not all safety tags serve the same purpose. A danger tag on a live wire isn’t the same as an inspection tag on a ladder or a scaffold tag at a construction site. Below is a practical guide to six essential safety tag types, how they should be used, and how to avoid the most common tagging mistakes.
“Do Not Operate” Lockout Tags

Do Not Operate tags are designed to prevent the use of equipment or machinery that is unsafe or undergoing maintenance. These lockout tags are used in conjunction with lockout devices, indicating that a machine or energy source has been isolated and should not be operated under any circumstances until it is cleared.
The incident I mentioned earlier, involving a technician who isolated a leaking high-pressure steam valve but used a makeshift tag, illustrates exactly what can go wrong. Without a proper “Do Not Operate” tag, the next crew overlooked the hazard and re-pressurized the line. The right action was taken, but the wrong tag failed to communicate it.
Barricade Tags
Barricade tags mark areas that are off-limits or pose temporary hazards, such as zones with open trenches, overhead work, chemical spills, or energized equipment. These tags are attached to barricades or temporary fencing, alerting workers and visitors to stay clear of hazardous areas until necessary precautions have been taken.
Unlike barricade signs, which are fixed or semi-permanent warning indicators, barricade tags are flexible and situation-specific. They often include custom details such as the type of hazard, the responsible supervisor or crew, and when the restriction expires or will be reviewed.
Scaffold Tags
Scaffold tags are specifically used in construction and industrial sites where scaffolding is in place to communicate whether the structure has passed inspection and is safe for use. Typically attached to scaffolds, these tags follow the standardized color-coding system to help crews quickly understand the safety status of scaffolds. Below is the scaffolding tag color meaning:
-
-
Green scaffolding tags mean the scaffold has been inspected and is safe for use without restrictions.
-
Yellow scaffolding tags signal limited or restricted use; there are safety concerns or conditions that require caution.
-
Red scaffolding tags indicate the scaffold is unsafe and must not be used until all required repairs or corrections are completed.
-
Ladder Tags
Ladder tags are attached to ladders and provide information about a ladder's condition, inspection status, and any usage restrictions. By clearly showing whether a ladder is safe to use, these tags help prevent accidents caused by damaged or uninspected equipment, especially in work environments where ladders are shared across teams.
For visibility, tags should be placed near the top rung or side rail, where they’re easily seen before use. Tags positioned near the bottom are often missed, reducing their effectiveness and increasing the chance of unsafe use.
Machine-Specific Tags
Machine or Equipment tags are used to provide the prior and current inspection status of a specific machine, tool, or piece of equipment. These tags help ensure that workers know whether a machine or tool is in service and ready for use, awaiting maintenance, or recently repaired or inspected. This prevents accidental use of equipment that’s unsafe or undergoing repair.
Use a machine risk assessment to determine which assets require permanent, visible safety tags. High-pressure, high-voltage, or moving parts are strong candidates.
Inspection Tags
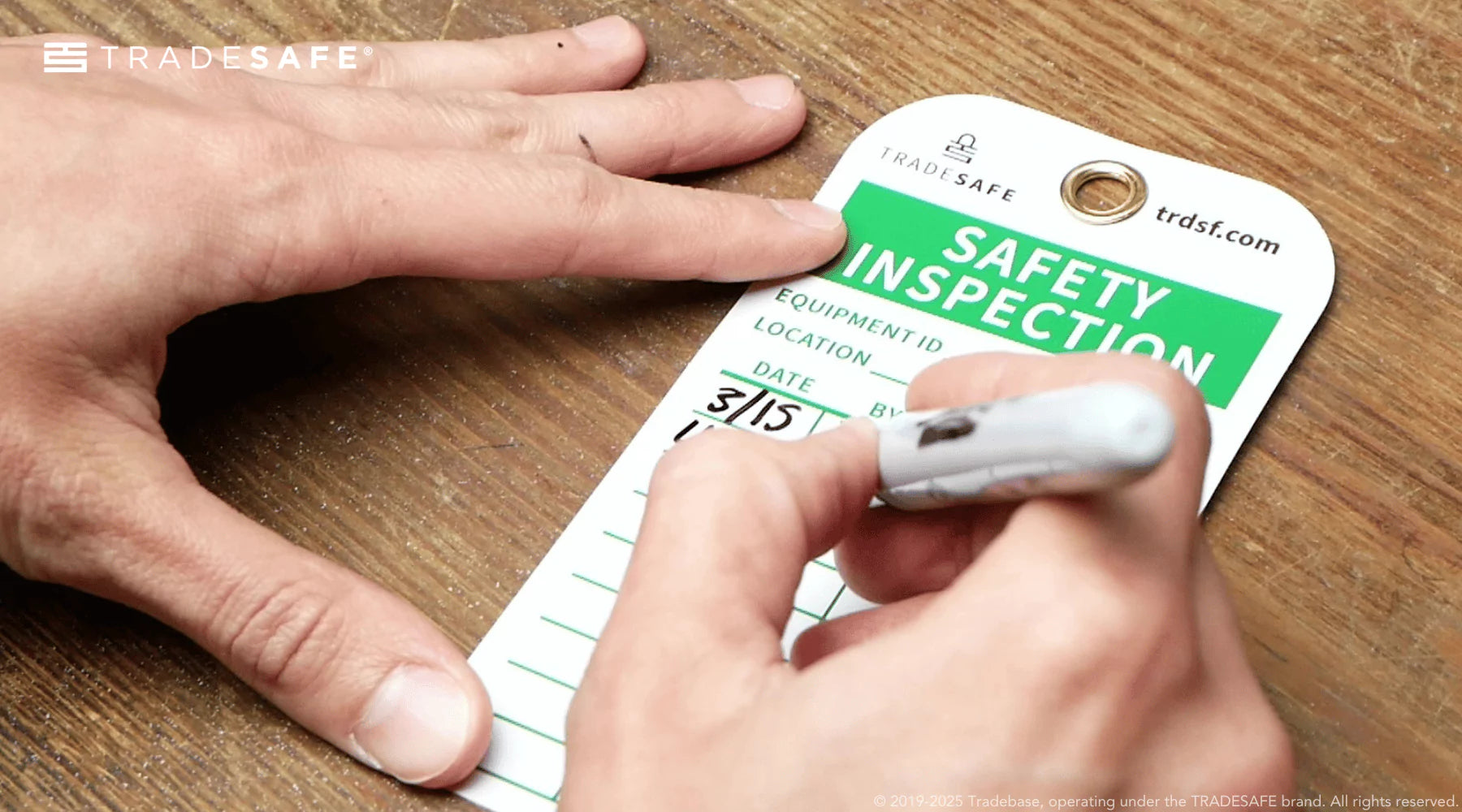
Inspection tags track maintenance, service dates, and condition of equipment, tools, and structures. These tags are commonly attached to lifting gear or safety equipment, such as fire extinguishers and eyewash stations. They serve as visual documentation of inspection status, and often include the date of the last inspection, technician initials, and service notes.
Digital Transformation in Safety Tagging
From QR codes to RFID chips and mobile inspection apps, the shift toward digital tagging is reshaping safety in occupational settings. Below are the latest innovations in digital tagging and how these technologies are changing the way OSHA safety tags are created, tracked, and used:
-
NFC and RFID Tags: Workers can scan a tag with a phone or reader and instantly see detailed equipment data and inspection history. RFID tags can also trigger alerts if equipment is moved, accessed, or energized without clearance.
-
AI-Powered Inspection Scheduling: Analyzes equipment usage, inspection history, and risk levels to optimize when inspections should happen. Instead of relying on fixed intervals, artificial intelligence and automation can flag high-use or high-risk assets that need attention sooner.
-
Mobile Apps for Tag Management: This eliminates the gap between field and office, allowing teams to scan or assign tags from the field, upload inspection photos and notes, receive alerts for overdue inspections or tag clearances, and access historical records instantly.
A colleague informed me about a mid-sized manufacturing plant in Illinois that transitioned the switch from paper inspection tags to a QR-based system linked to their CMMS (Computerized Maintenance Management Systems). The change wasn’t complicated, but it made a big difference. With digital tags tracking inspections and syncing updates in real time, they went 18 months without a single inspection-related equipment failure—their longest stretch of uninterrupted uptime in five years.
At first glance, digital tagging may seem more expensive, but that depends on how you measure cost. While RFID tags or app subscriptions carry upfront costs, they often save money long-term by reducing equipment downtime, preventing accidents, automating audit trails, and improving inspection accuracy.
How to Build a Culture of Tag Compliance
No matter how advanced your tags are or how well your procedures are written, a safety tagging system only works if people actually use it. Here’s how to create a culture where safety tags are used correctly every time:
-
-
Develop a Training Program that Sticks: Teach every employee what each type of tag means, when to use it, and what to do if something isn’t tagged properly. But don’t stop there. Good training is interactive, job-specific, and repeatable.
-
Make Tagging Accessible: Keep tag stations well-stocked, organized, and easily accessible on the job site. Workers are far more likely to follow protocol when the tools are clear, available, and usable without guesswork.
-
Use Behavioral Psychology to Reinforce Good Habits: People ignore tags when the tagging process slows them down, or they’ve never seen consequences for skipping it. Shift that mindset by reinforcing why tagging matters. Share near-miss reports during toolbox talks.
-
Gamify Tag Compliance: Many companies have seen success by turning compliance into a measurable goal. Small rewards, recognition, and healthy competition can transform safety from an obligation into genuine engagement.
-
Track KPIs for Tagging Programs: Measure what drives results, and use this data to identify weak spots, retraining needs, and areas where the system may be slowing people down unnecessarily.
-
Common Violations and How to Avoid Them

Let’s face it: just about everyone has walked past a panel or machine tagged with a handwritten sign on torn cardboard that reads “Do Not Operate. Under Repair.” It's a quick fix. It's easy. And it’s wrong. While the intention is right, the execution misses the mark in more ways than one.
This kind of makeshift tag isn’t durable, isn’t standardized, and doesn’t meet OSHA requirements for safety tags. Worse, it leaves too much room for miscommunication or total disregard. Anyone can write anything on a piece of cardboard.
So why does this keep happening? Usually, it's a mix of convenience and lack of awareness. Teams may not have immediate access to official tags or might believe a handwritten sign gets the message across just fine. But cutting corners on tagging can lead to serious consequences: unexpected startups, injuries, or worse.
The fix? Keep standardized, weather-resistant safety tags readily available wherever equipment service or repair is common. Train teams to use them, and set clear expectations: no more cardboard, no more guesswork. If it’s not official, it’s not safe.
Maintenance and Replacement of Safety Tags
Regular maintenance and replacement of tags are necessary to ensure their visibility, accuracy, and compliance. Tags or safety signage in the workplace that are faded, torn, water-damaged, or no longer reflect the current status of equipment must be removed and replaced immediately. This includes both temporary tags and long-term ones.
FAQs on Safety Tags
Are safety tags mandatory in all workplaces?
Safety tag requirements may vary depending on the industry and local regulations. It is essential to consult relevant safety guidelines and regulations to determine the specific requirements for safety tags in a particular workplace.
Can safety tags replace other safety measures, such as training and PPE?
No, safety tags should complement other safety measures, such as training programs and the use of appropriate PPE. Safety tags serve as visual reminders and warnings, but should not be relied upon as the sole means of ensuring workplace safety.
Can safety tags be customized for specific workplace needs?
Yes, safety tags can be customized to include company logos, additional warnings, or specific instructions relevant to a particular workplace. However, it's crucial to ensure that the customization does not compromise the clarity and effectiveness of the safety message.
Can I use one universal tag for multiple hazards?
It's not recommended. Using one tag for all hazards can create confusion or lead to misinterpretation. Different tag types and colors should be used to reflect the nature and severity of each hazard clearly.
What's the best way to train non-English speakers on tag meanings?
Use multilingual tags, clear symbols, and hands-on demonstrations. Supplement written training with visual aids and, where possible, provide instruction in workers’ primary languages to ensure full understanding.